ロードレースに勝つため、世界最高峰を制したトラックバイクの知見に基づき作られたアンカーの新作「RP9」。ディスクブレーキを装備し、空力性能を高め、フレームセットで前作のRS9sよりも軽量に仕上がったロードバイクだ。
RP9を駆り、Jプロツアー第11戦で勝利を挙げた今村駿介(チームブリヂストンサイクリング) photo:Satoru Kato
得意とするのは、あらゆる状況。目指したのはワンデーレースからステージレースまで、あらゆる環境が入り乱れるロードレースで勝てること。走りの性能はもちろん、走らないときの使い勝手にまで、現実の状況に沿ってこだわり尽くした一台だ。
開発時にテストしたのは、このバイクで実際に勝利しているTEAM BRIDGESTONECyclingのチーム員たち。アンカーならではの技術と日本人ならではの心遣いで現実にした、日本人こそ使いやすい性能と走りのフィーリング。それがRP9の真髄である。
スポーツ車両設計開発課の中村さん(左)と商品企画課の村河さん(右)。RP9を作り上げた中心人物お二人に話を聞いた photo:Nobuhiko Tanabe
ブリヂストンサイクルの工場の中にある扉の奥に「カーボンラボ」はあった。とても整理された空間だった。
工具が並ぶメカニックスペース。プリプレグと呼ばれるカーボンの生シートが保管される-20度の冷凍庫。カーボンシートを切り出すカッティングプロッター。フレームの型を削り出すマシニングセンタ。そしてカーボンフレームの成形窯であるオートクレーブがある。どれも広い空間の中に余裕を持って置かれている。いろんなものが雑然と並んだ、昔ながらの「製作所」のイメージとはほど遠い。
カーボンラボの中心的存在であるオートクレーブ。カーボンフレームを成形する窯だ photo:Nobuhiko Tanabe
真空状態にして加熱 photo:Nobuhiko Tanabe
オートクレーブにはTEAM BRIDGESTONECyclingのメンバーのサインがあった photo:Nobuhiko Tanabe
カーボンラボを案内してくれたのは、このRP9の開発に携わったブリヂストンサイクルのスポーツ車両設計開発課・中村隆志さん。
「この型の中にプリプレグを積層して、袋に入れて空気を抜いて、真空にしながら加熱するんです」。
このカーボンラボができたのは2015年。そこから2年後の2017年、UCIトラック世界選手権で世界を制したトラックフレームの本格開発が始まった。
「このラボができて、本当にいろんな時間が短縮できました。開発プロセスのサイクルが短くなるということは、多くの試験ができるということなんですね。試作したフレームに一枚だけプリプレグを貼って、その違いを検証するという細かな試験もできたんです。またそのシート一枚の違いを言い当てる選手の鋭さにも驚きました」(中村さん)
ラボ内ではマシニングセンタが稼働中だった photo:Nobuhiko Tanabe
実際にラボ内で製作されたRP9試作用のフレーム型 photo:Nobuhiko Tanabe
熱の入ったインタビューはとても長いものに。その内容をお伝えする photo:Nobuhiko Tanabe
つまりアンカーの強みはここにある。開発者のイメージをそのままその場で形にできるカーボンラボ。その試作品の物理的なデータをPROFORMATの中枢である(株)ブリヂストンの基盤技術部門で取り、さらにそのデータを実際の感覚としてチームの選手たちがテストする。この3つが連携し、求めるイメージ、感覚、データに素早くたどり着ける。
RP9の解説の中から浮かんできた疑問を、開発に携わった方々に回答してもらった。話を聞いたのは、前出の中村さんと、全体の企画を担当した、商品企画課・村河裕紀さん。話にも熱が入り、実際はとても長くなったが、ここではその二人の回答をまとめ、要点をお伝えしていく。
2種類のトラックバイク開発経験をロードバイクに落とし込み、RP9は誕生した photo:Nobuhiko Tanabe
Q:オールラウンダーのバイクを目指した理由は?
もともと、エアロロードの開発に迫られていたというのはありました。ですが目標設定に向けた基礎研究を行うなか、純粋なエアロロードにしてしまうと、レースにおいて使える場面が限られてしまうことがわかり、オールラウンドに1台で戦えるバイクに軌道修正しました。
オールラウンダーと純粋なエアロロードバイクとを隔てるポイントが、「重量面で不利にならないレベルまで軽くすること」、そして「適度な剛性バランスを持たせること」でした。そこをベースに空力性能を煮詰めていきました。
この前にあったトラックバイクの開発、特に短距離種目用の「PRZ」では、感覚と物理現象との関係性を確かにすることに力を尽くしました。その進化系であるRP9の開発は、前作RS9の開発時のテーマだった「前に進むバイク」を、さらに突き詰めたものになっています。
「"前に進むバイク(RS9)"を、さらに突き詰めたもの。それがRP9です」 photo:Nobuhiko Tanabe
Q:ラインアップを増やさず、一台のオールラウンドにしたのは?
ステージレースを想定すると、1つのコースでも登りや平地など様々な環境が入り乱れていることも多いため、何かの性能に特化させるよりも1台で戦える方が適していると考えています。また、チームや市場からも1台ですべてを賄えるバイクの要望が出ているのも理由です。
チームから初期に出たのが、軽くて反応がいいフレームがいい、でした。軽ければ軽い方がいいということ。空力は良ければいい、ということでした。空力よりも重量と剛性のほうがより優先度が高かったのです。
それに「乗り心地がヌルい」のは嫌だとも。つまりフィーリングの良しあしも重要な要素ということです。選手もやはり人間なので、タイムが早くても加速感の乏しい、進む感のないフィーリングのバイクは好まれません。「物理的に進むこと」と「進む感覚」を両立しなければならないのが開発上も難しかったポイントです。
現場での整備性を考慮した専用ステムを開発。これはチームからの大きな要望だった photo:Nobuhiko Tanabe
RP9の専用ステム。レース現場やショップでのメンテナンスを考慮した photo:Nobuhiko Tanabe
付属するトップキャップを用いることでノーマルステムも使用可能だ photo:Nobuhiko Tanabe
Q:使いやすさという点で、チーム員から出てきた要望は?
レースの現場でポジションを変えるケースが多くあるので、そこが面倒なのは困る、というのがありました。スペーサーを変えたいだけなのに、ブレーキケーブルなどを切らなくてはいけないのはやめて欲しい、と。それはチームのメカニックの強い要望だったので、レース機材として守っていかなければいけない、ヘッド・ステム周りの設計はとても重要だと考えていました。
Q:シートポストクランプなども小物も独自設計を?
フレームを設計しながら、小物類の設計も進めました。結局、専用設計のパーツでないと、空力性能と実際の使い勝手を両立できなかったんです。シートポストも、インテグラルではなく調整できるエアロポストにしました。空輸することを考えて、ポストの中にバッテリーを入れているので、付け外しする場面でも簡単に作業できます。
素早くモノを作り、それを評価する。カーボンラボがそのプロセスサイクルを早めた photo:Nobuhiko Tanabe
Q:PROFORMATというアンカー独自の技術には、どこまでが含まれる?
特定の技術というより、開発のプロセス自体をPROFORMATと呼んでいます。
例えばCFD(数値流体力学)や風洞実験での結果をもとにした空力解析。FEM(有限要素法)でのカーボン積層のシミュレーションなどを使っての構造、材料の設計。そのやりとり全体がPROFORMATです。
トラックバイク開発の初期から、選手の言葉を形にしていくという作業を、2017年から3年近く続けてきました。その中で、彼らの言葉と物理的な現象、そこを行ったり来たりしながら通訳していくプロセスがPROFORMATである、という感覚でした。
選手に言われたことを仮説立てて、実際のものとして設計して、ラボで現実のものとして試作して、試乗してもらう。そういうR&Dのサイクル自体がPROFORMATの根幹にあるものです。具体的なところが複雑に絡み合っているんですね。
Q:カーボンラボが自社にあることでの大きな利点とは?
素早くモノを作り、それを評価し、また試作するというサイクルを早く行うことを目標に活動しています。全てを自分たちでできるようになったことで、修正がより素早くできる、というのが一番大きいでしょうか。
それに加えて、PROFORMATで蓄積したデータや経験を元に、より高精度なシミュレーション(CFD、FEM)を行うことができ、試作の精度がどんどん上がっていきます。そのため、目標に辿り着くまでの時間、回数が少なくできる。目標の設定も具体性を持ってきちんとできるのが、開発としては嬉しいところでした。
空力を重視する部分、軽さを追求する部分。フレームの各部において最適な形状をあてはめていったという photo:Nobuhiko Tanabe
Q:ロードバイクの場合、空力上、最も気にすべきポイントは?
特に前方部が効いてきますね。ですから前面投影面積をできるだけ小さくします。なのでバイク前面に関しては空力重視で形状を煮詰めています。特にフロントフォークは、空力上で大幅に工夫しています。その他にも風洞実験で、シートチューブ、BB周りといった部分での検証を繰り返し、良さそうな結果を全体に適応させる、というプロセスを行いました。
ですが、そこで気にしたのが剛性が失われたらだめ、というところ。トラック開発の時に最も重視したところでした。
Q:「RS9sと比べ、平均250wで5km走行した場合、約14秒のタイム短縮(注)につながる」とのこと、これはなかなかに大きな数字ですが...?
実際に風洞実験でやってみると、本当にそういう差になってしまうんです。ただこれはベストの状況なので。実際に走るとケースバイケースだと思います。RS9sは、空力性能に関して改善の余地があったので。
※試験条件:RP9はプロトタイプ(490mm/SHIMANODURA-ACE R9170ペダルレス/EASTON EC90 AERO/DT SWISS ARC1100 50)/RS9s市販仕様にホイール(Shimano WH-9000-C50)装着
※タイムシミュレーションは風洞実験での実測値を元に簡易的に算出したもの。
※バイクの差はブリヂストンサイクルで実施した風洞試験におけるRP9とRS9sの完成車をヨー角±0度で計測した実測値を使用し、ライダー相当のCdAはブリヂストンサイクルで実施した複数の風洞試験の実測値を使用。
※250w:約43㎞/h巡行(競技志向のライダー想定)
カーボンラボ内には無数のテストフレーム(これらはトラックバイク)が置かれていた photo:Nobuhiko Tanabe
これは3Dスキャナー。乗車ポジションなど各部寸法を計測する photo:Nobuhiko Tanabe
こちらはカーボンシート(プリプレグ)の保管庫。-20度で保管するという photo:Nobuhiko Tanabe
Q:「高強度カーボン素材、T1100を使用した」とのこと、これらはどんな機能を利点を持つ素材?
まずは強度ですね。カーボン繊維の中でも強度が高い素材で、そして弾性率も適度にある。フレームとして考えると、強度も気にすることになるんですが、そのため高強度のカーボン(T1100)を使うことでプリプレグを貼る枚数を少なくできて、重量を軽くできました。
Q:「適切なレイアップを検証、無駄のない構成を実現」とのこと、具体的にどこで無駄を省いた?
具体的にどこ、というのはなく、全体的に、ですね。トータルでプリプレグの枚数を、減らせるところを減らす、というのを積み重ねていきました。
Q:小物込みでの重量が1,360g(注)。もう少し軽くもできたかと思うが、ここに留めたのは?
剛性と空力とのバランスを鑑みて、適度なところで留めた、ところです。剛性と空力と重量、これら性能は基本的なところでトレードオフ、あちらを立てればこちらが立たず、という関係になるんですね。
注:※フレーム+フォーク+小物類(ステム、シートポスト、スルーアクスル含まず)、フレームサイズ490mm
「日本のレースで、実際に勝てるバイクを目指しました」 photo:Nobuhiko Tanabe
Q:「トラックバイクで培った剛性」と聞くと、どうしても硬い、とイメージしてしまうが振動吸収性はどうか?
硬くなることで振動吸収性がネガになることがありますが、既に実戦投入しているチームからも特に問題ないというフィードバックを受けています。エアロ効果を求めた形状でロードを作ると、どうしても縦方向に硬くなる傾向があるので、我々も気にしてはいたんですが、実用上問題ないレベルに仕上げられたと思っています。
Q:ロードレースに必要な剛性とは? どう硬く、どう柔らかくある必要があった?
選手が気にしていたのはやはりアタック時の反応でした。大きな出力で一気に踏んだ際にロスなく進むかどうかが重要だと考えています。またヘッド周りなどのハンドリングについても、下りなどでシビアに効いてくるポイントです。
Q:レース用ということだが、一般ユーザーが踏み負けてしまう、そんなことはない?
脚質次第だとは思いますが、比較的大きな出力で踏める選手向けに開発をしています。ですが、ほどほどの出力でもRP9の持つ気持ちよさは十分味わって頂けると思います。
社内の試乗でも「踏む気にさせられる」「速く走りたくなる」バイクだ、という声が出ています。踏んで気持ちいい、というのはロードバイクの楽しさの根源だと思っています。
「踏む気にさせられる」「速く走りたくなる」バイク。それがRP9だ photo:Nobuhiko Tanabe
今後RP9に乗るライダーの多くは、例えば来月のレースで結果を残したい、と切に願う選手であるはずだ。実際に世界に挑戦できるのは、ほんのひと握りだろう。今目の前にいるひとりの日本の選手が、次のロードレースで勝てるように、と願ったバイク。そのために、綿密な計算と細かな調整を繰り返し作られたオールラウンダー。RP9はそのために作られた、という印象である。「世界を制した技術」を、単なるスローガンにしていない。
質疑応答が終わり、ここで藤野智一さんが口を開いた。元プロレーサーで、今はプロショップ「なるしまフレンド」に勤務する藤野さんには、このRP9を試乗してもらうため、この場に同行してもらっていたのだ。
「(まだテストしていない段階で)今良いな、と思えるのは価格ですよね。このスペックでフレームセット49万5千円(税込)は、だいぶコストを抑えてきた印象ですよね」。
さすが、実際にお客さんに接するショップからの視点である。この価格も、日本のブランドであるアンカーならではだと藤野さんは見抜く。性能、使い勝手、そして価格とすべてが現実的なのだ。RP9は日本のレースに勝てる性能を、レース出場のために日々練習を積み、週末を費やす選手が手にできるものに落とし込んでいる。
次回はRP9のインプレッションを紹介。アンカーを知り尽くした藤野智一さん(なるしまフレンド)の言葉に注目してほしい photo:Nobuhiko Tanabe
「使ってもらって、なんぼです」と中村さんは、言った。その通りである。次回は、藤野智一さんに、実際に使ってもらい、そのインプレを聞かせてもらう。
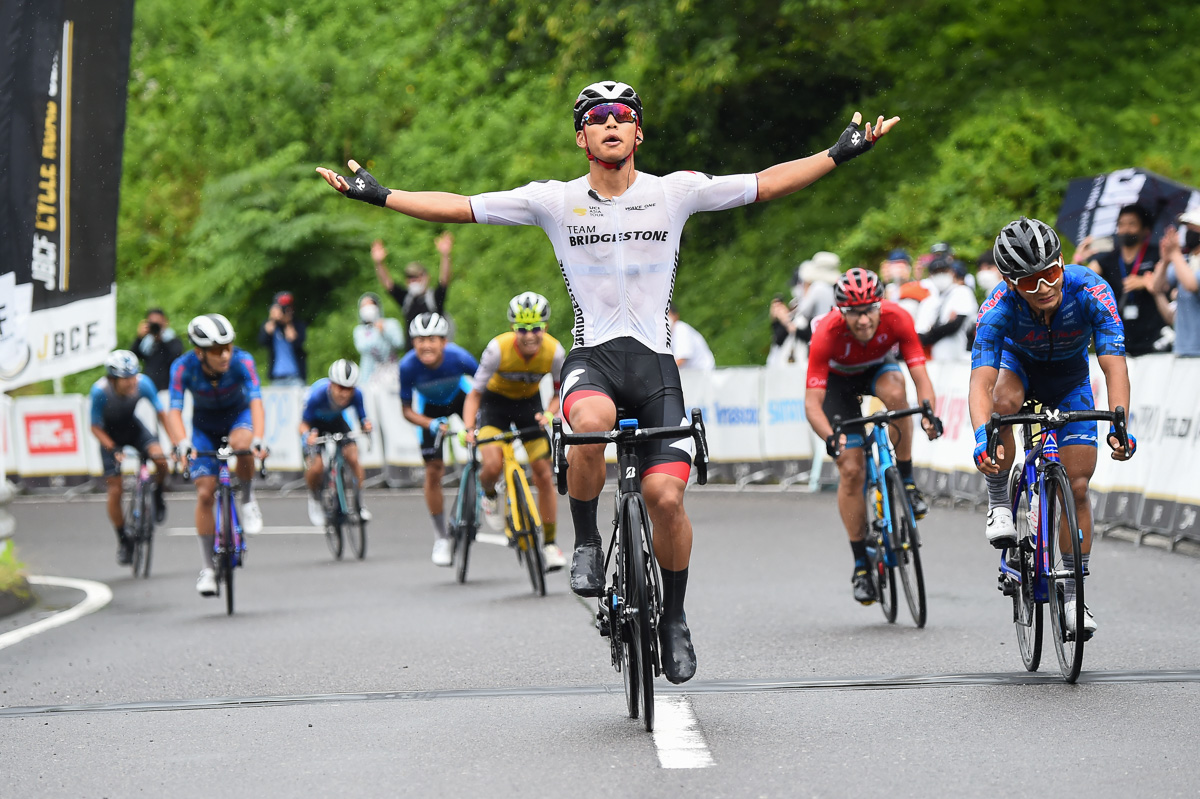
得意とするのは、あらゆる状況。目指したのはワンデーレースからステージレースまで、あらゆる環境が入り乱れるロードレースで勝てること。走りの性能はもちろん、走らないときの使い勝手にまで、現実の状況に沿ってこだわり尽くした一台だ。
開発時にテストしたのは、このバイクで実際に勝利しているTEAM BRIDGESTONECyclingのチーム員たち。アンカーならではの技術と日本人ならではの心遣いで現実にした、日本人こそ使いやすい性能と走りのフィーリング。それがRP9の真髄である。
本社内のカーボンラボを訪問。細やかな試作作りが可能な施設があった
RP9を深く知る上で、取材班は埼玉県上尾市にあるアンカーの母体、ブリヂストンサイクルに向かった。RP9の開発拠点となった「カーボンラボ」をこの取材のために公開してくれたからだ。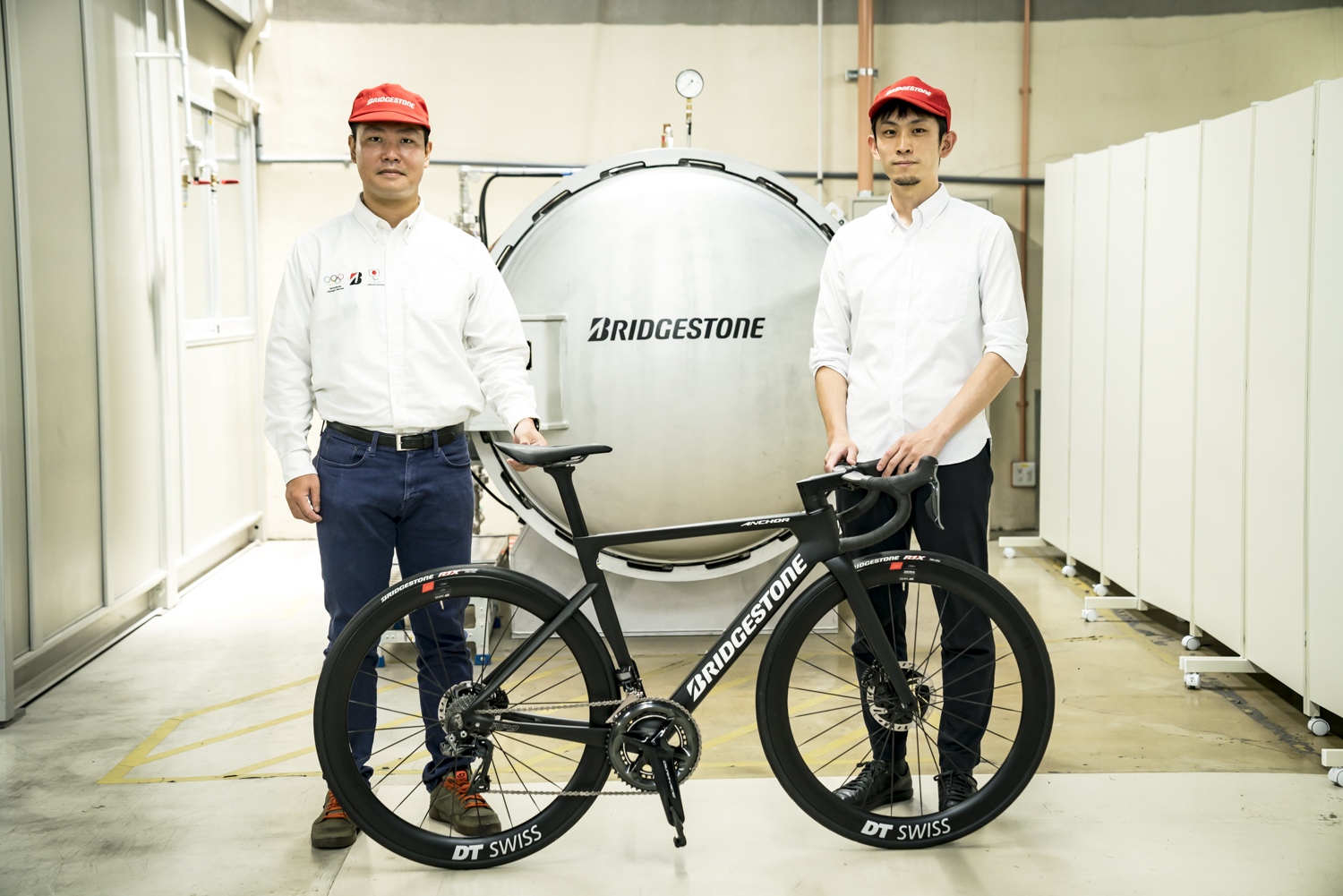
ブリヂストンサイクルの工場の中にある扉の奥に「カーボンラボ」はあった。とても整理された空間だった。
工具が並ぶメカニックスペース。プリプレグと呼ばれるカーボンの生シートが保管される-20度の冷凍庫。カーボンシートを切り出すカッティングプロッター。フレームの型を削り出すマシニングセンタ。そしてカーボンフレームの成形窯であるオートクレーブがある。どれも広い空間の中に余裕を持って置かれている。いろんなものが雑然と並んだ、昔ながらの「製作所」のイメージとはほど遠い。
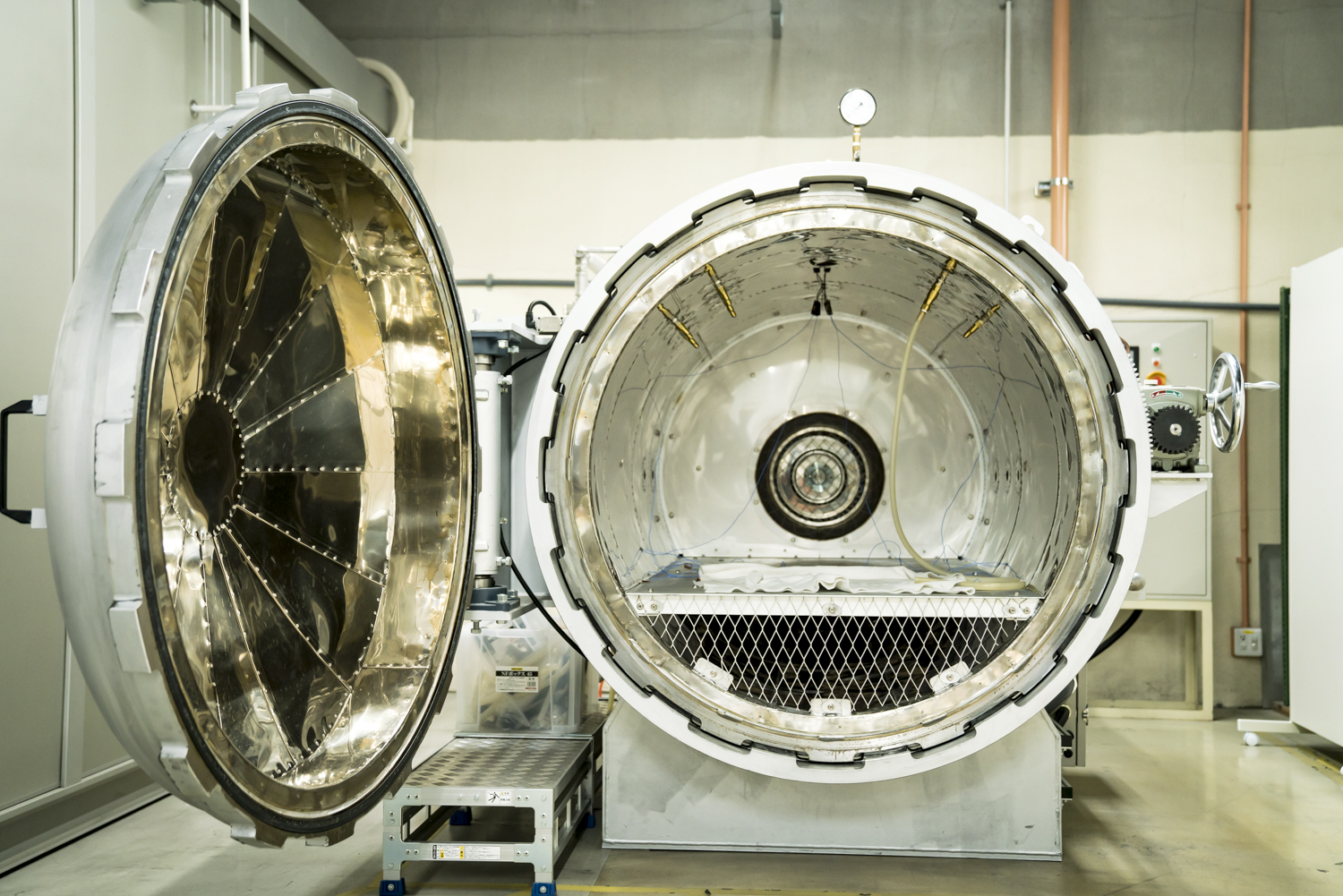
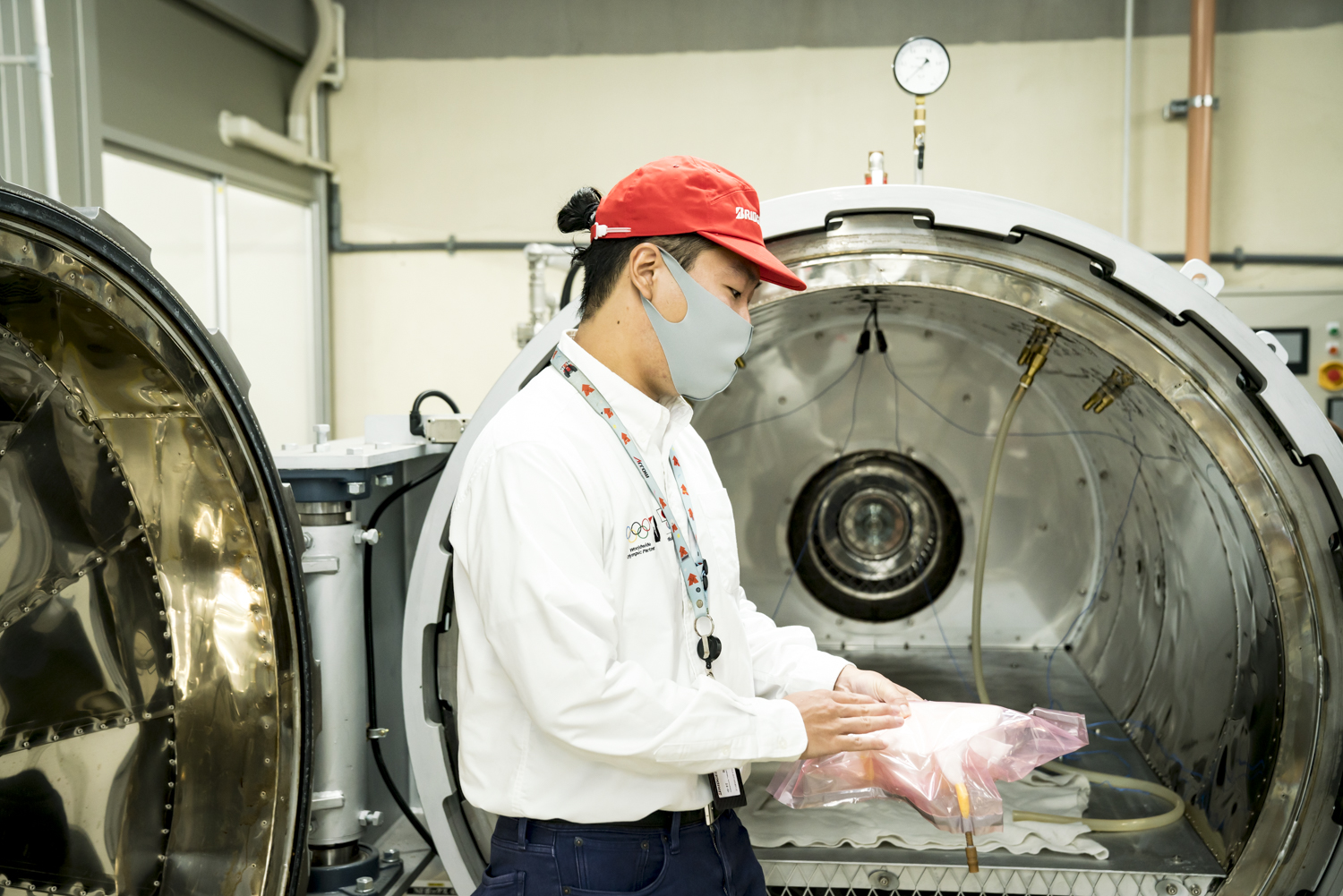
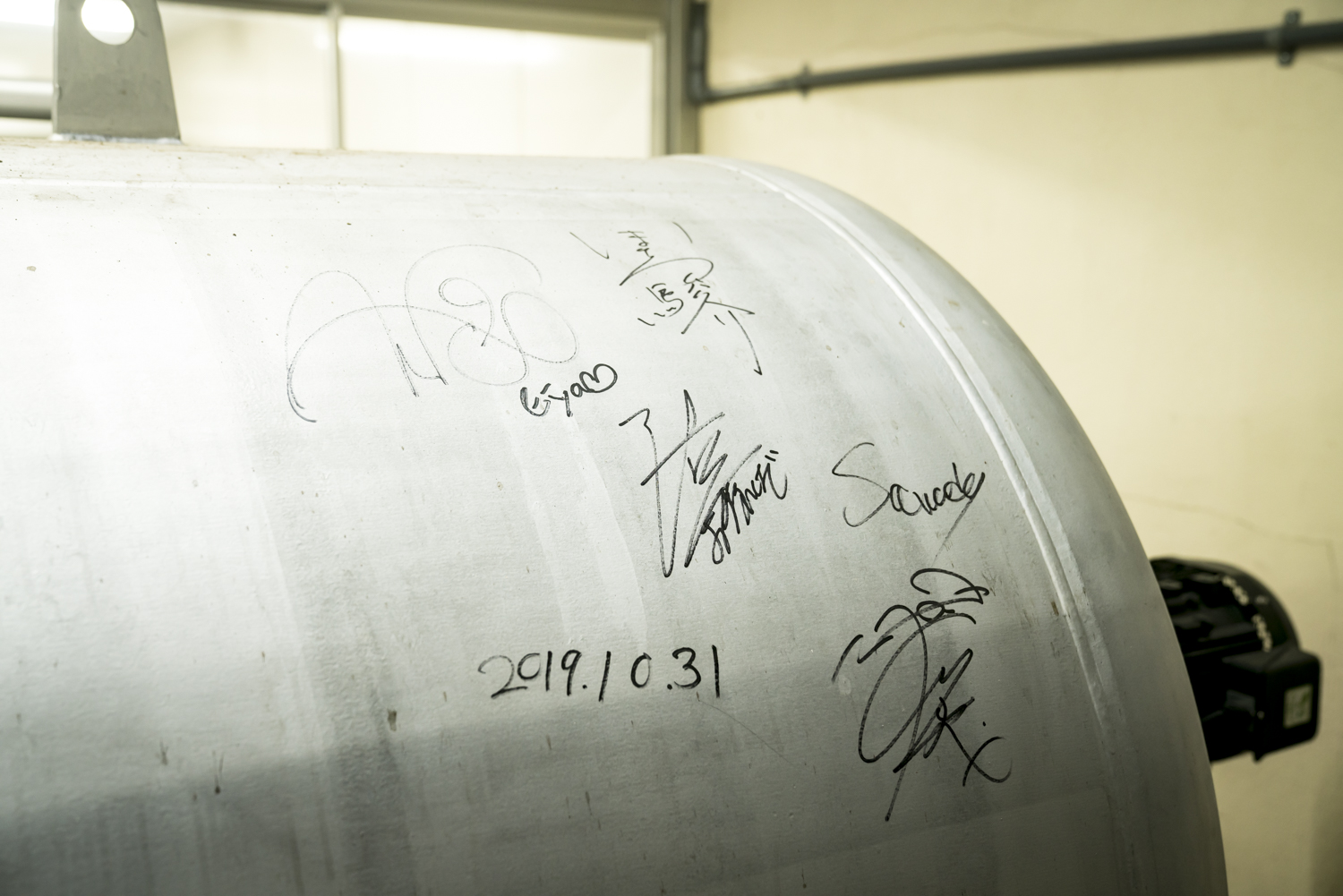
カーボンラボを案内してくれたのは、このRP9の開発に携わったブリヂストンサイクルのスポーツ車両設計開発課・中村隆志さん。
「この型の中にプリプレグを積層して、袋に入れて空気を抜いて、真空にしながら加熱するんです」。
このカーボンラボができたのは2015年。そこから2年後の2017年、UCIトラック世界選手権で世界を制したトラックフレームの本格開発が始まった。
「このラボができて、本当にいろんな時間が短縮できました。開発プロセスのサイクルが短くなるということは、多くの試験ができるということなんですね。試作したフレームに一枚だけプリプレグを貼って、その違いを検証するという細かな試験もできたんです。またそのシート一枚の違いを言い当てる選手の鋭さにも驚きました」(中村さん)
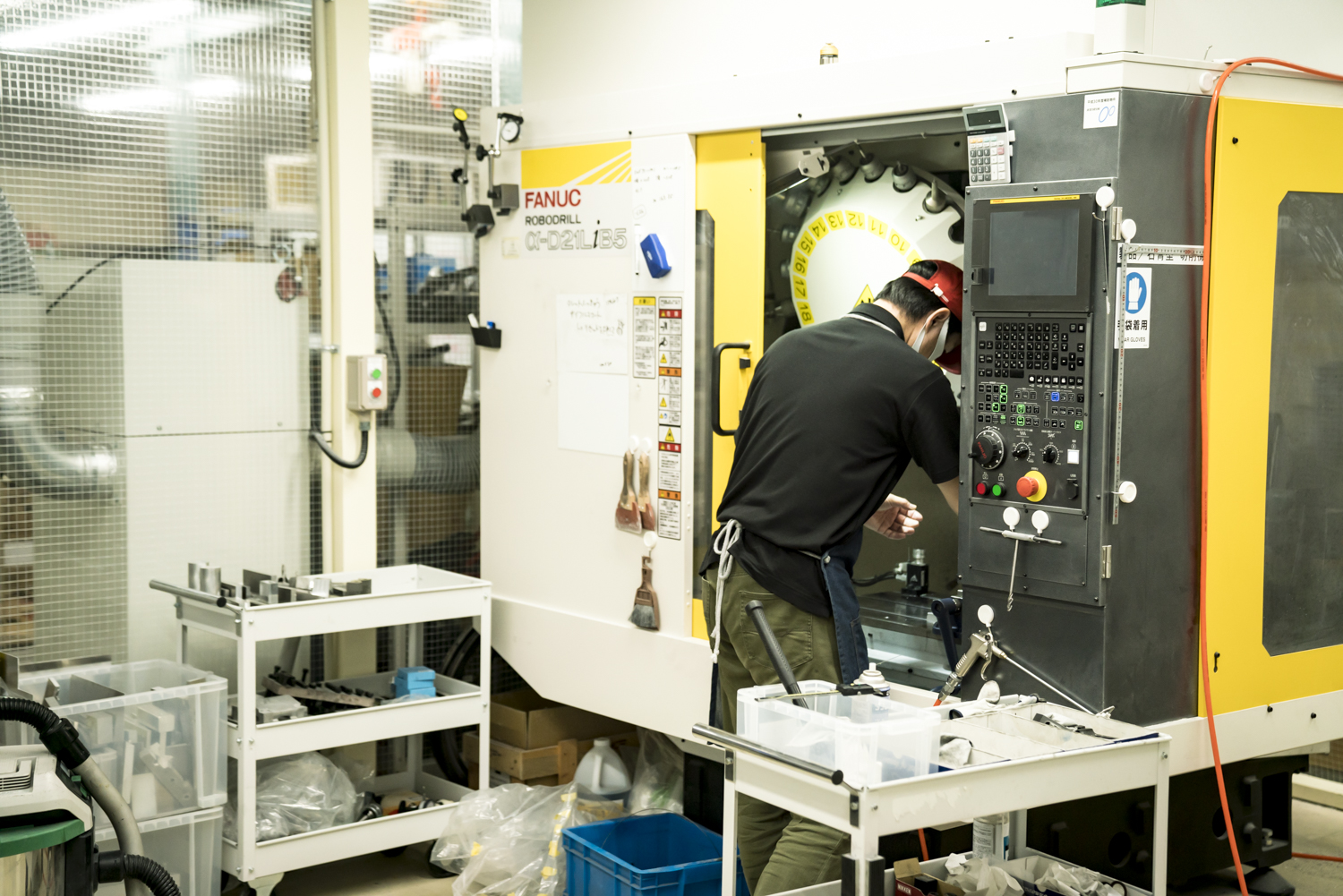
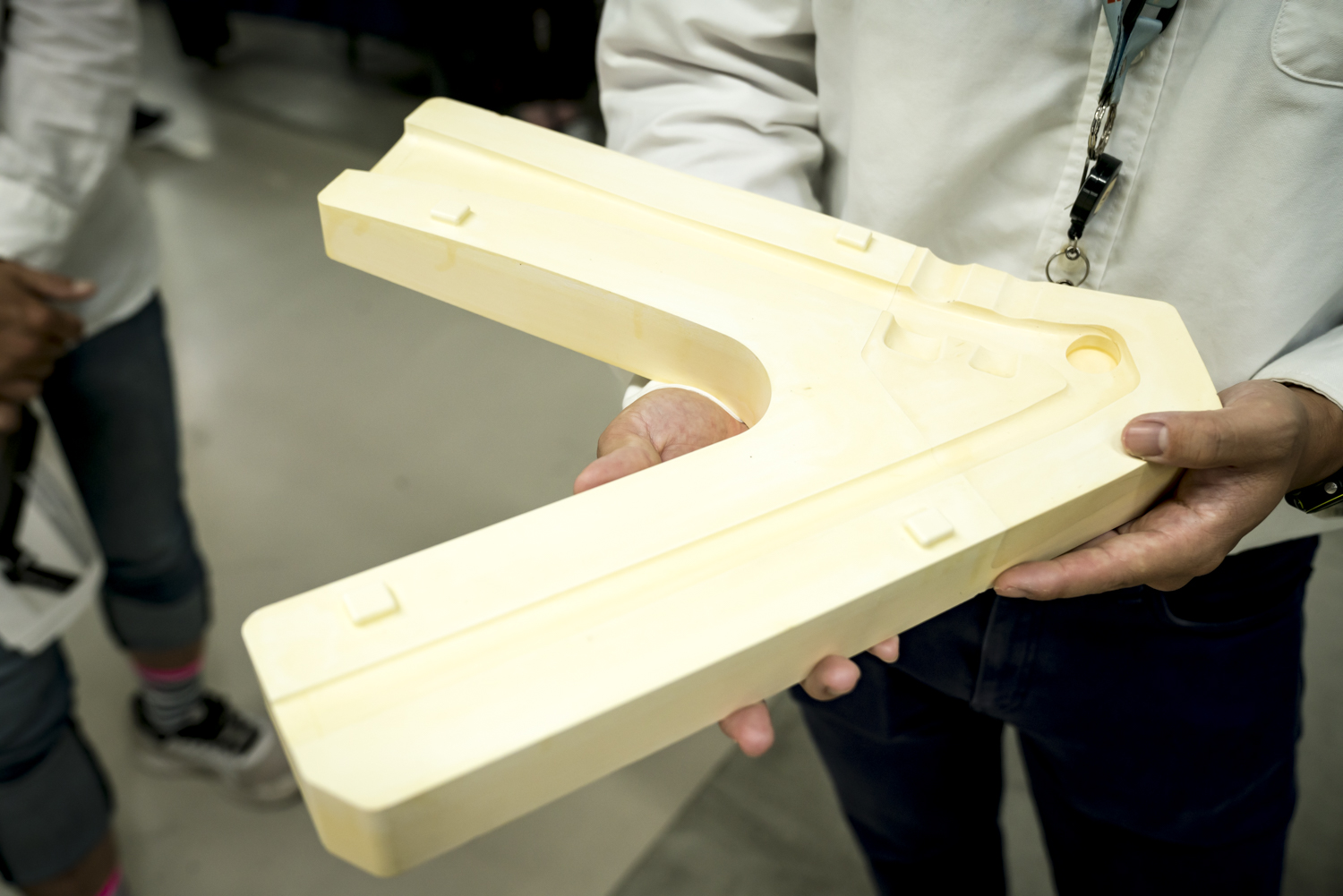
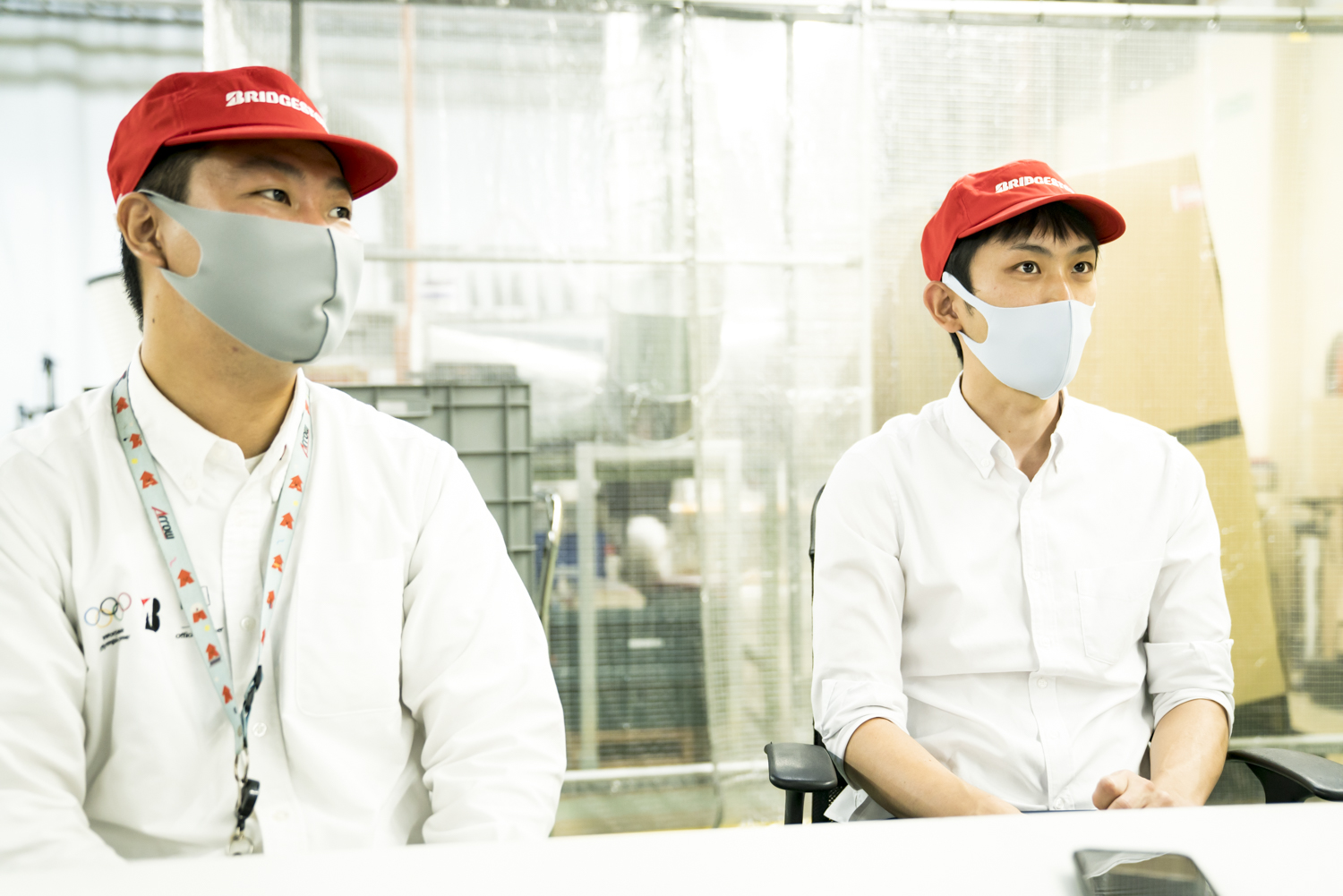
つまりアンカーの強みはここにある。開発者のイメージをそのままその場で形にできるカーボンラボ。その試作品の物理的なデータをPROFORMATの中枢である(株)ブリヂストンの基盤技術部門で取り、さらにそのデータを実際の感覚としてチームの選手たちがテストする。この3つが連携し、求めるイメージ、感覚、データに素早くたどり着ける。
RP9の解説の中から浮かんできた疑問を、開発に携わった方々に回答してもらった。話を聞いたのは、前出の中村さんと、全体の企画を担当した、商品企画課・村河裕紀さん。話にも熱が入り、実際はとても長くなったが、ここではその二人の回答をまとめ、要点をお伝えしていく。
開発者インタビュー
チームからも市場からも「一台ですべてを賄いたい」という声があった
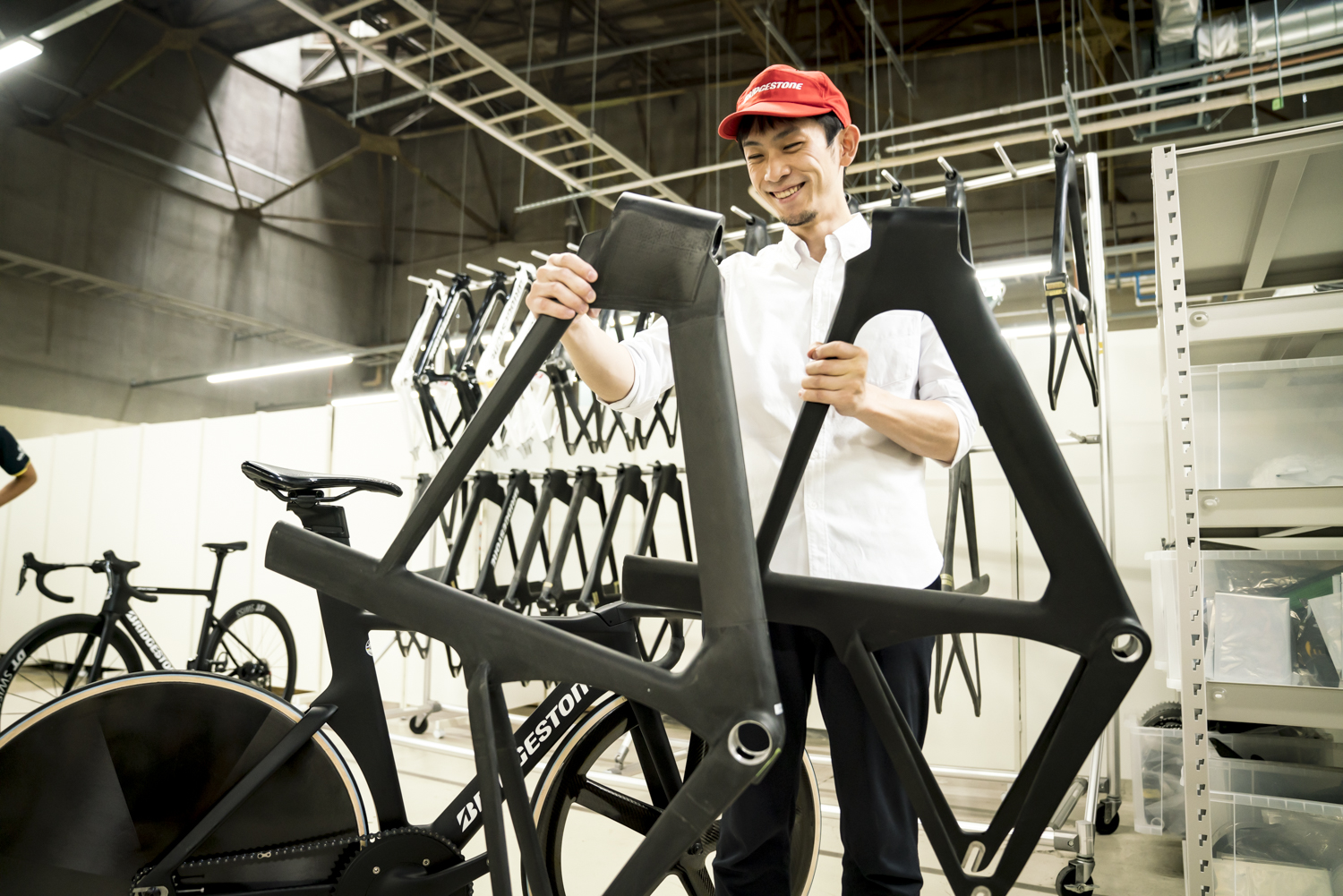
Q:オールラウンダーのバイクを目指した理由は?
もともと、エアロロードの開発に迫られていたというのはありました。ですが目標設定に向けた基礎研究を行うなか、純粋なエアロロードにしてしまうと、レースにおいて使える場面が限られてしまうことがわかり、オールラウンドに1台で戦えるバイクに軌道修正しました。
オールラウンダーと純粋なエアロロードバイクとを隔てるポイントが、「重量面で不利にならないレベルまで軽くすること」、そして「適度な剛性バランスを持たせること」でした。そこをベースに空力性能を煮詰めていきました。
この前にあったトラックバイクの開発、特に短距離種目用の「PRZ」では、感覚と物理現象との関係性を確かにすることに力を尽くしました。その進化系であるRP9の開発は、前作RS9の開発時のテーマだった「前に進むバイク」を、さらに突き詰めたものになっています。
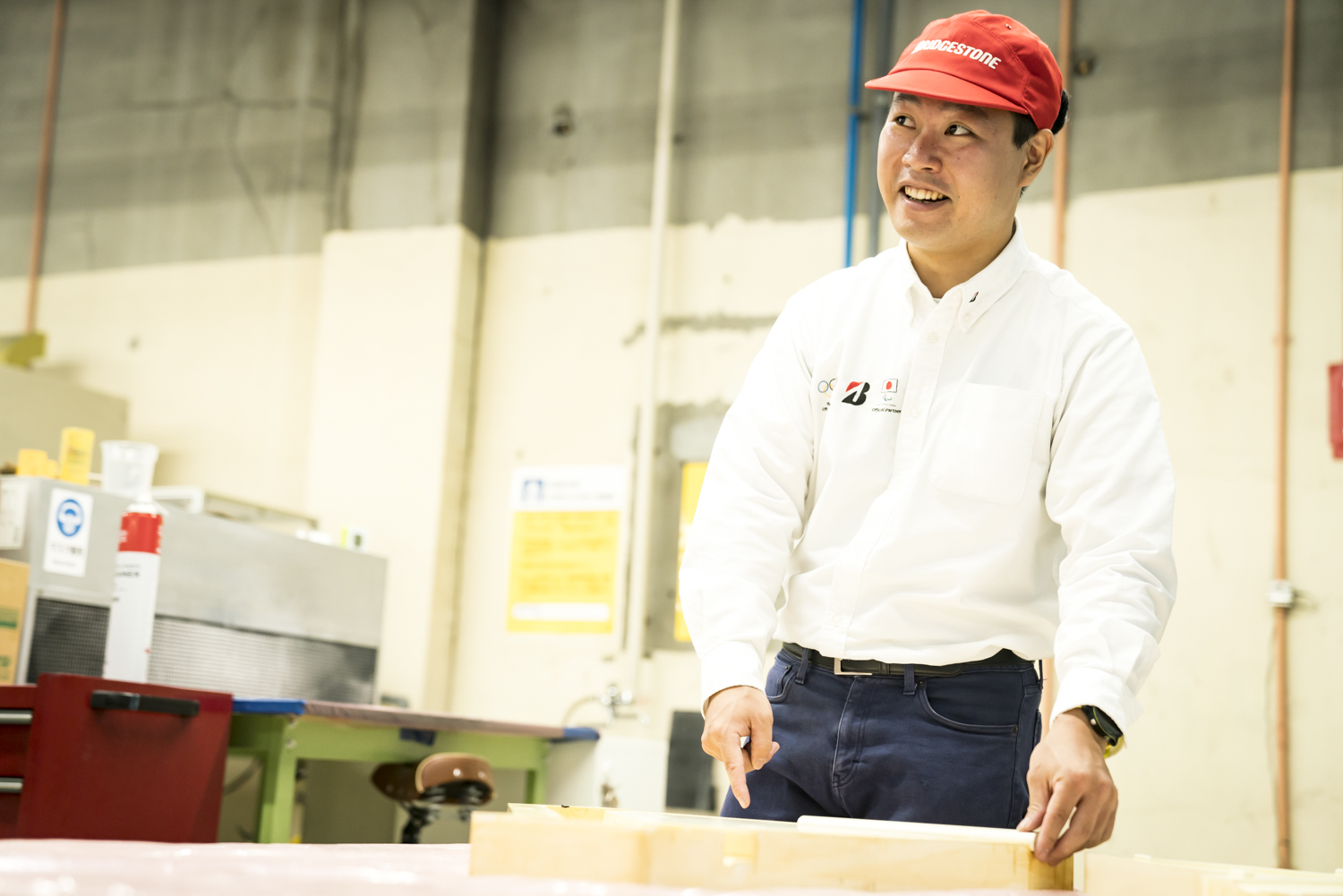
Q:ラインアップを増やさず、一台のオールラウンドにしたのは?
ステージレースを想定すると、1つのコースでも登りや平地など様々な環境が入り乱れていることも多いため、何かの性能に特化させるよりも1台で戦える方が適していると考えています。また、チームや市場からも1台ですべてを賄えるバイクの要望が出ているのも理由です。
選手からは「ヌルいものはイヤ」というオファーが
Q:チーム員から性能としてのオファーには、どんなものがあった?チームから初期に出たのが、軽くて反応がいいフレームがいい、でした。軽ければ軽い方がいいということ。空力は良ければいい、ということでした。空力よりも重量と剛性のほうがより優先度が高かったのです。
それに「乗り心地がヌルい」のは嫌だとも。つまりフィーリングの良しあしも重要な要素ということです。選手もやはり人間なので、タイムが早くても加速感の乏しい、進む感のないフィーリングのバイクは好まれません。「物理的に進むこと」と「進む感覚」を両立しなければならないのが開発上も難しかったポイントです。
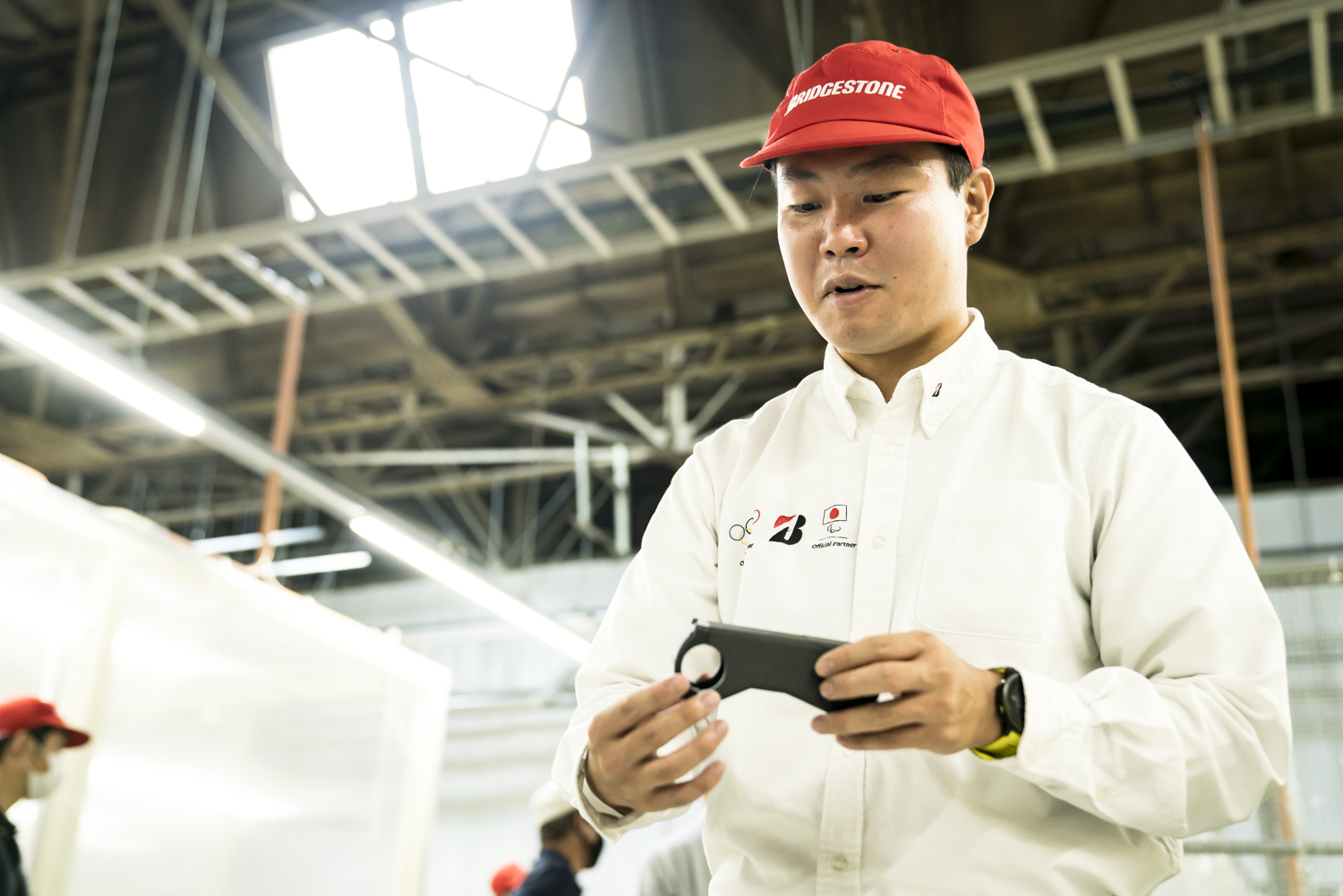
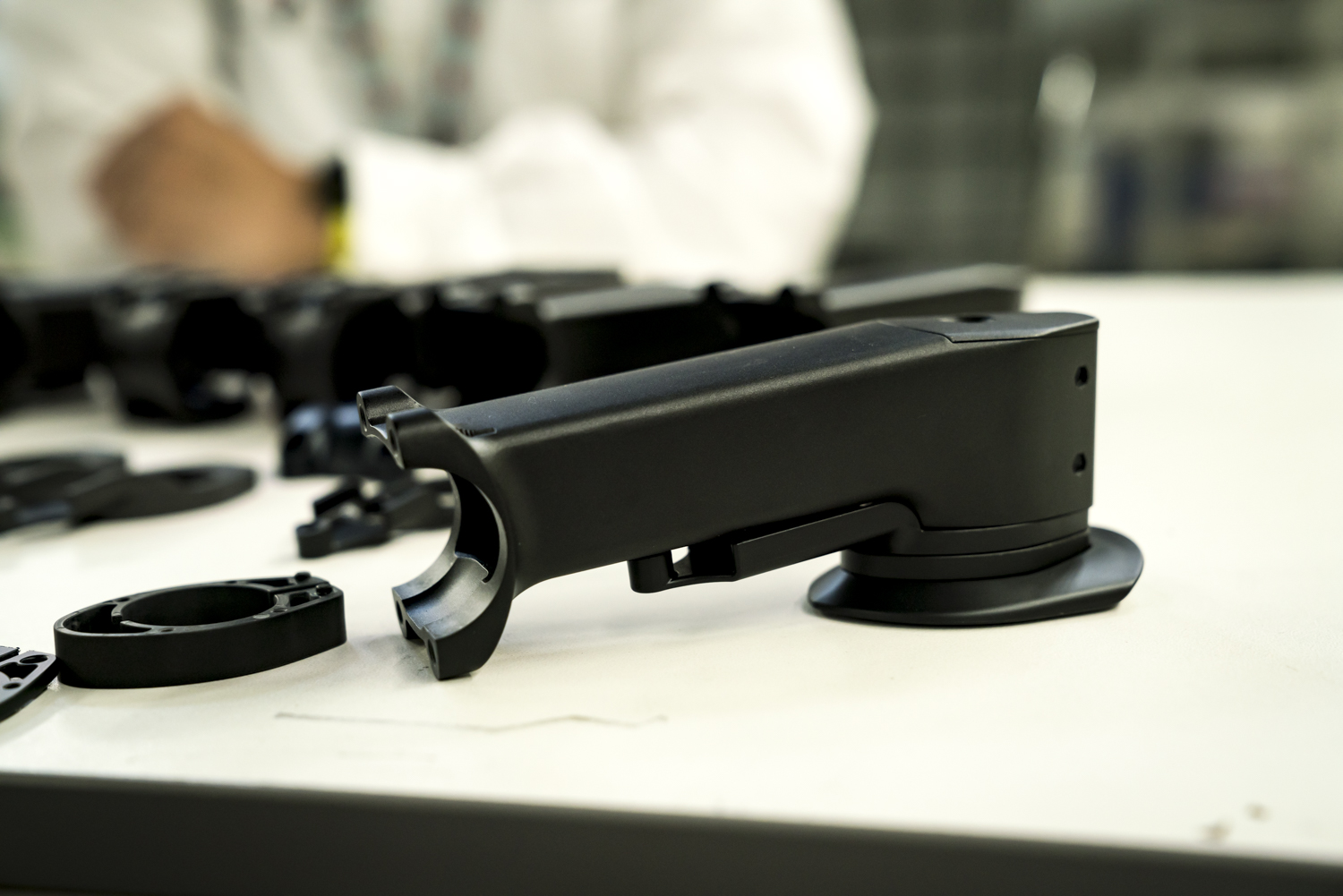
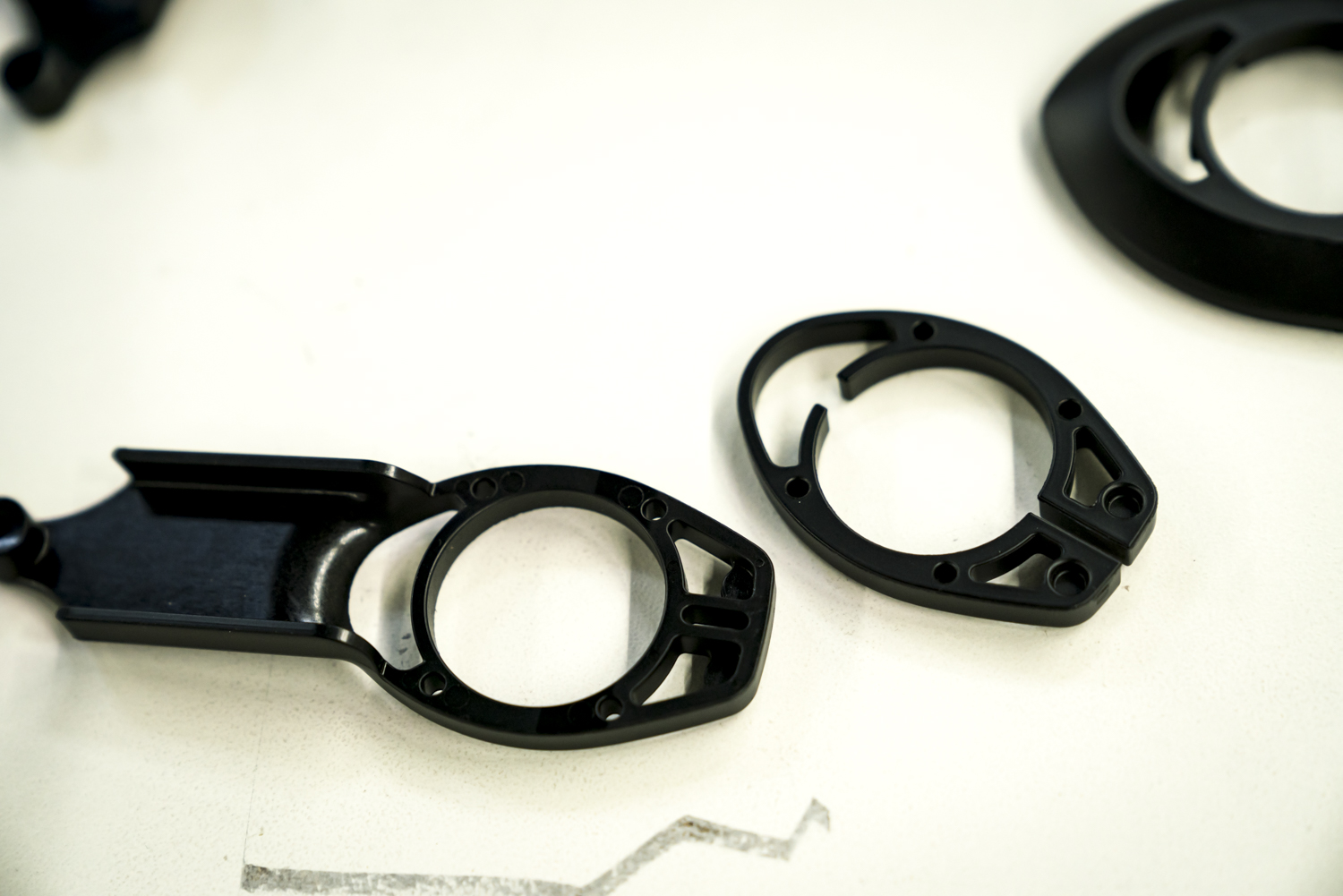
Q:使いやすさという点で、チーム員から出てきた要望は?
レースの現場でポジションを変えるケースが多くあるので、そこが面倒なのは困る、というのがありました。スペーサーを変えたいだけなのに、ブレーキケーブルなどを切らなくてはいけないのはやめて欲しい、と。それはチームのメカニックの強い要望だったので、レース機材として守っていかなければいけない、ヘッド・ステム周りの設計はとても重要だと考えていました。
Q:シートポストクランプなども小物も独自設計を?
フレームを設計しながら、小物類の設計も進めました。結局、専用設計のパーツでないと、空力性能と実際の使い勝手を両立できなかったんです。シートポストも、インテグラルではなく調整できるエアロポストにしました。空輸することを考えて、ポストの中にバッテリーを入れているので、付け外しする場面でも簡単に作業できます。
「PROFORMAT」とは開発のプロセス自体。選手の言葉を通訳するもの
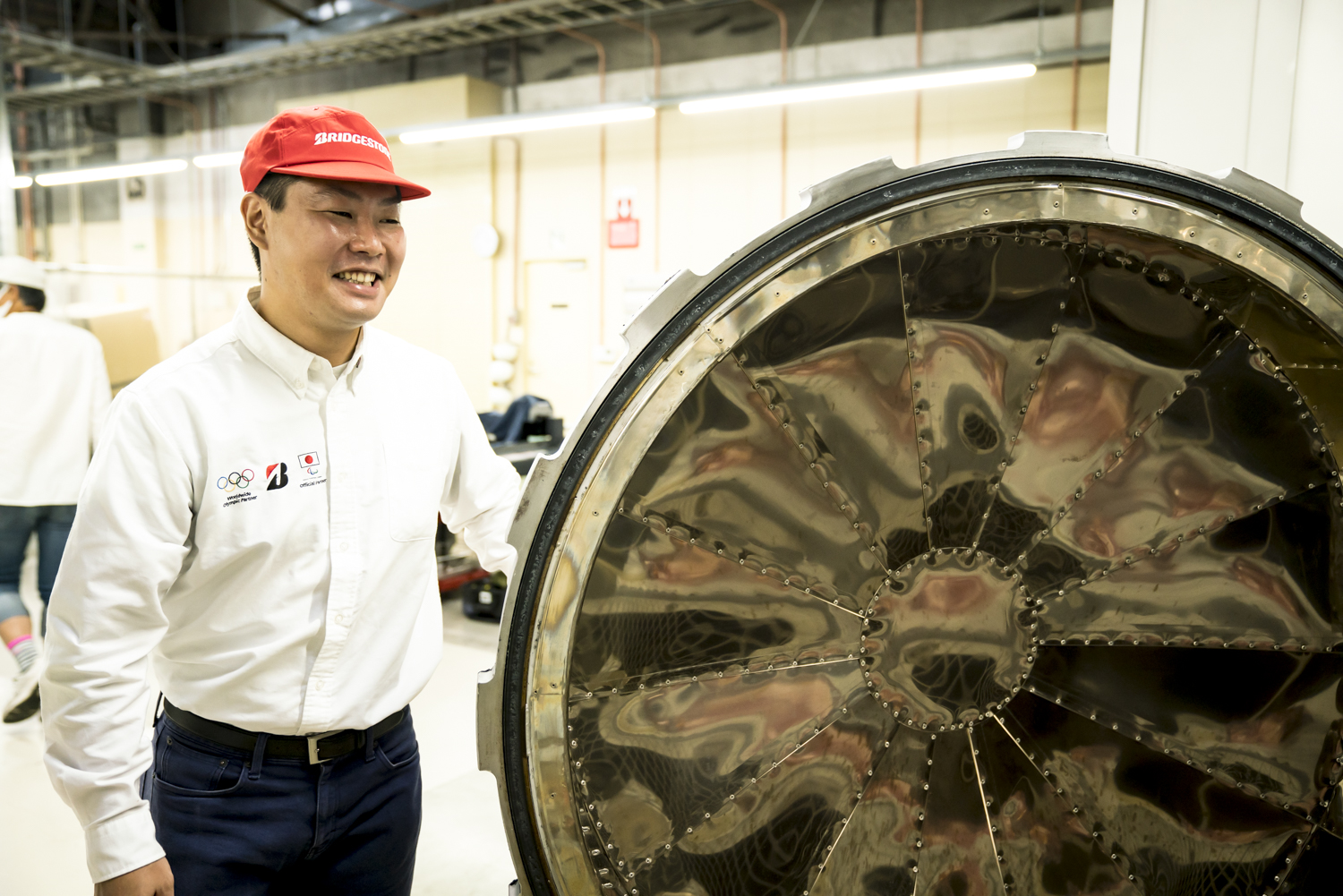
Q:PROFORMATというアンカー独自の技術には、どこまでが含まれる?
特定の技術というより、開発のプロセス自体をPROFORMATと呼んでいます。
例えばCFD(数値流体力学)や風洞実験での結果をもとにした空力解析。FEM(有限要素法)でのカーボン積層のシミュレーションなどを使っての構造、材料の設計。そのやりとり全体がPROFORMATです。
トラックバイク開発の初期から、選手の言葉を形にしていくという作業を、2017年から3年近く続けてきました。その中で、彼らの言葉と物理的な現象、そこを行ったり来たりしながら通訳していくプロセスがPROFORMATである、という感覚でした。
選手に言われたことを仮説立てて、実際のものとして設計して、ラボで現実のものとして試作して、試乗してもらう。そういうR&Dのサイクル自体がPROFORMATの根幹にあるものです。具体的なところが複雑に絡み合っているんですね。
Q:カーボンラボが自社にあることでの大きな利点とは?
素早くモノを作り、それを評価し、また試作するというサイクルを早く行うことを目標に活動しています。全てを自分たちでできるようになったことで、修正がより素早くできる、というのが一番大きいでしょうか。
それに加えて、PROFORMATで蓄積したデータや経験を元に、より高精度なシミュレーション(CFD、FEM)を行うことができ、試作の精度がどんどん上がっていきます。そのため、目標に辿り着くまでの時間、回数が少なくできる。目標の設定も具体性を持ってきちんとできるのが、開発としては嬉しいところでした。
「空力」について:まずは前面投影面積、そして細かな積み重ねを
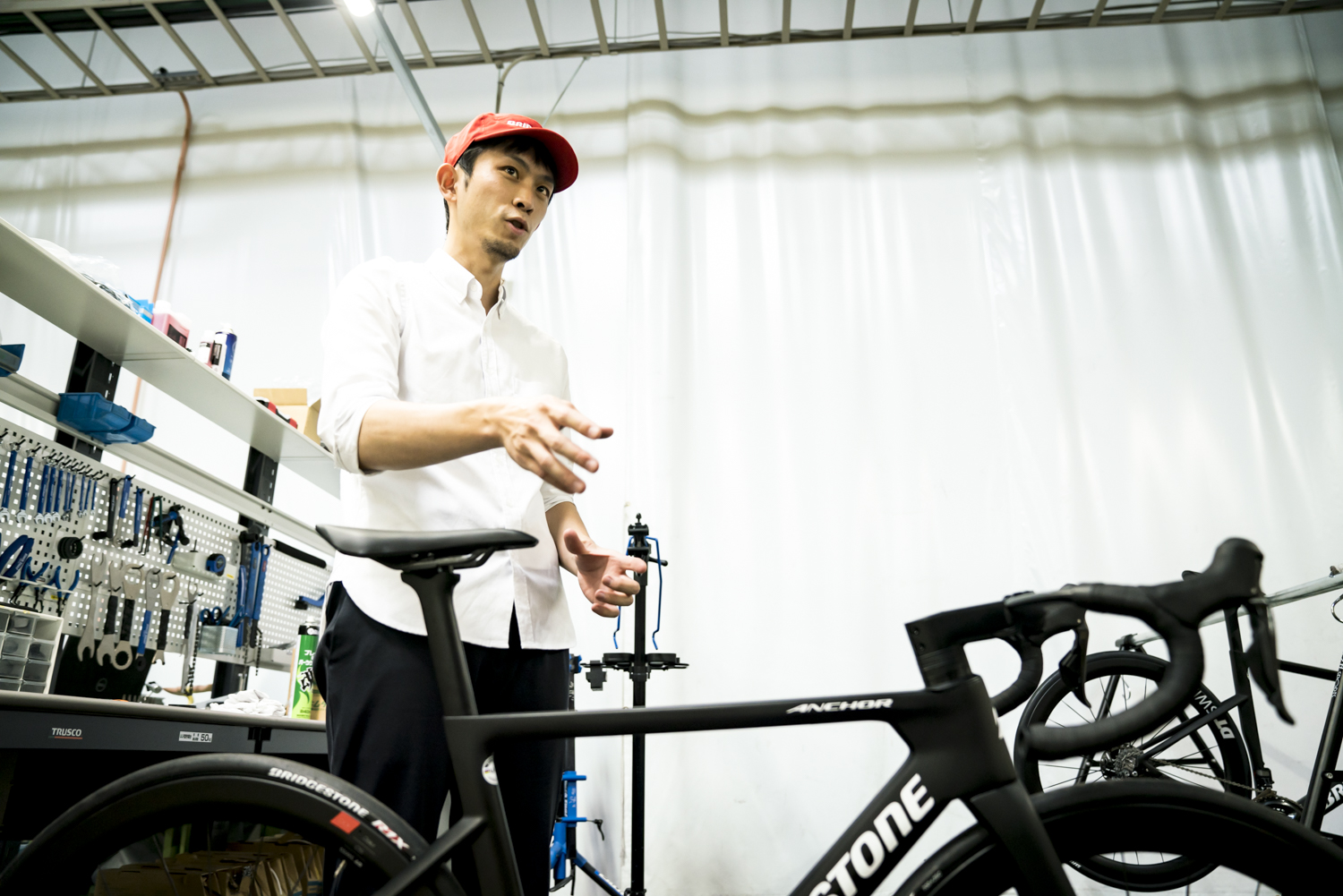
Q:ロードバイクの場合、空力上、最も気にすべきポイントは?
特に前方部が効いてきますね。ですから前面投影面積をできるだけ小さくします。なのでバイク前面に関しては空力重視で形状を煮詰めています。特にフロントフォークは、空力上で大幅に工夫しています。その他にも風洞実験で、シートチューブ、BB周りといった部分での検証を繰り返し、良さそうな結果を全体に適応させる、というプロセスを行いました。
ですが、そこで気にしたのが剛性が失われたらだめ、というところ。トラック開発の時に最も重視したところでした。
Q:「RS9sと比べ、平均250wで5km走行した場合、約14秒のタイム短縮(注)につながる」とのこと、これはなかなかに大きな数字ですが...?
実際に風洞実験でやってみると、本当にそういう差になってしまうんです。ただこれはベストの状況なので。実際に走るとケースバイケースだと思います。RS9sは、空力性能に関して改善の余地があったので。
※試験条件:RP9はプロトタイプ(490mm/SHIMANODURA-ACE R9170ペダルレス/EASTON EC90 AERO/DT SWISS ARC1100 50)/RS9s市販仕様にホイール(Shimano WH-9000-C50)装着
※タイムシミュレーションは風洞実験での実測値を元に簡易的に算出したもの。
※バイクの差はブリヂストンサイクルで実施した風洞試験におけるRP9とRS9sの完成車をヨー角±0度で計測した実測値を使用し、ライダー相当のCdAはブリヂストンサイクルで実施した複数の風洞試験の実測値を使用。
※250w:約43㎞/h巡行(競技志向のライダー想定)
軽さについて:強度のあるカーボン素材を使い、貼る枚数を減らしていった
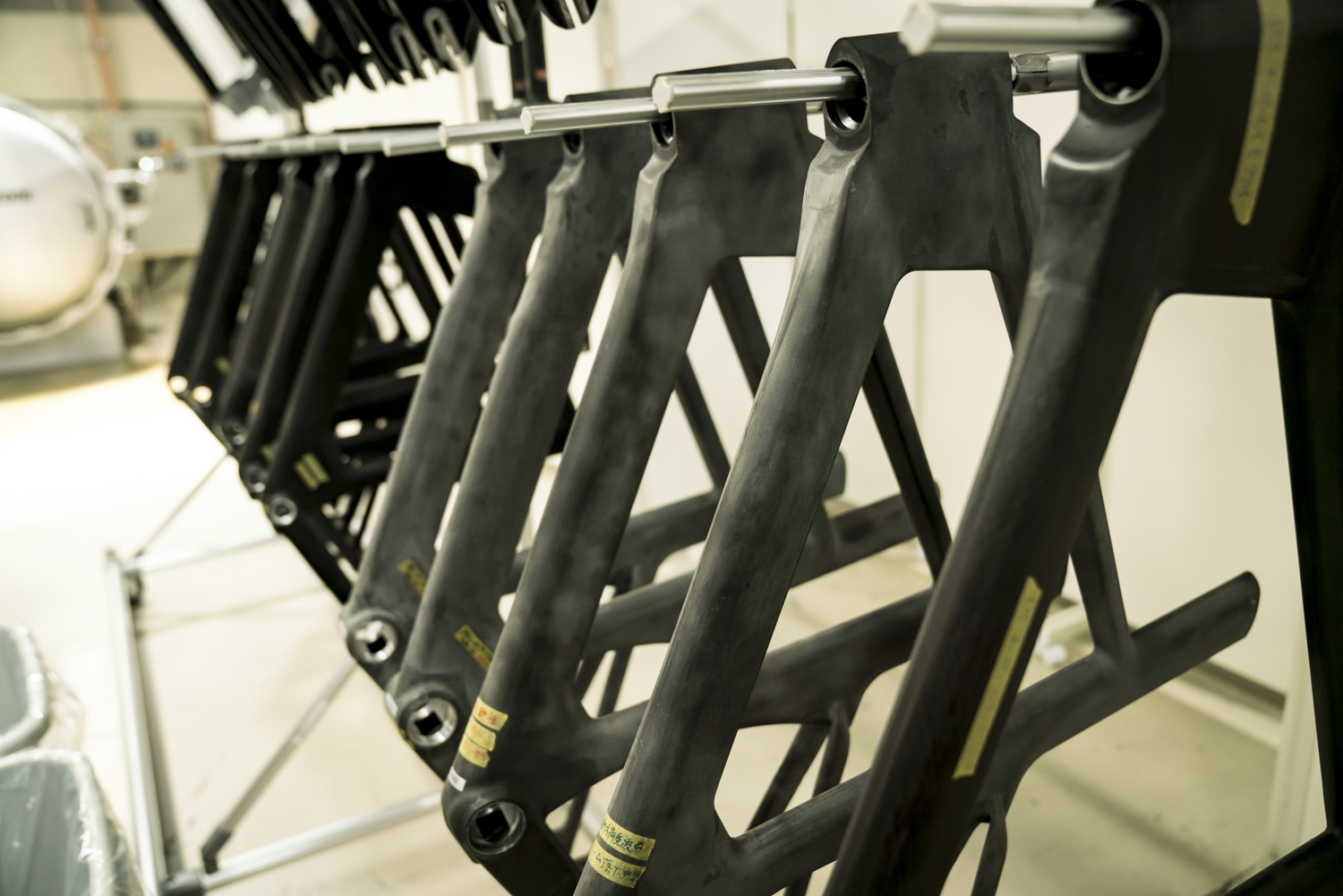

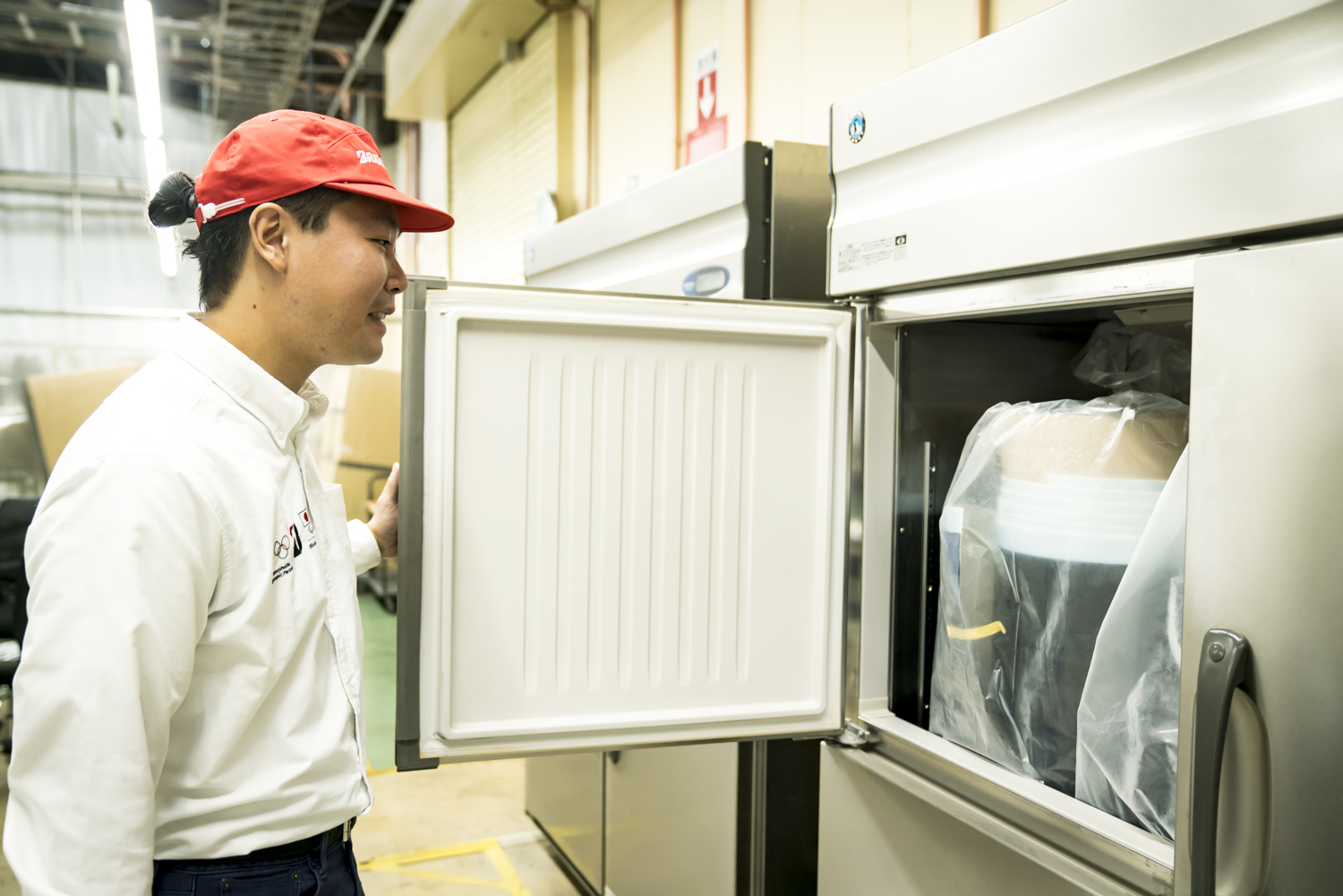
Q:「高強度カーボン素材、T1100を使用した」とのこと、これらはどんな機能を利点を持つ素材?
まずは強度ですね。カーボン繊維の中でも強度が高い素材で、そして弾性率も適度にある。フレームとして考えると、強度も気にすることになるんですが、そのため高強度のカーボン(T1100)を使うことでプリプレグを貼る枚数を少なくできて、重量を軽くできました。
Q:「適切なレイアップを検証、無駄のない構成を実現」とのこと、具体的にどこで無駄を省いた?
具体的にどこ、というのはなく、全体的に、ですね。トータルでプリプレグの枚数を、減らせるところを減らす、というのを積み重ねていきました。
Q:小物込みでの重量が1,360g(注)。もう少し軽くもできたかと思うが、ここに留めたのは?
剛性と空力とのバランスを鑑みて、適度なところで留めた、ところです。剛性と空力と重量、これら性能は基本的なところでトレードオフ、あちらを立てればこちらが立たず、という関係になるんですね。
注:※フレーム+フォーク+小物類(ステム、シートポスト、スルーアクスル含まず)、フレームサイズ490mm
剛性について:日本のレースで実際に必要な性能を剛性として求めた
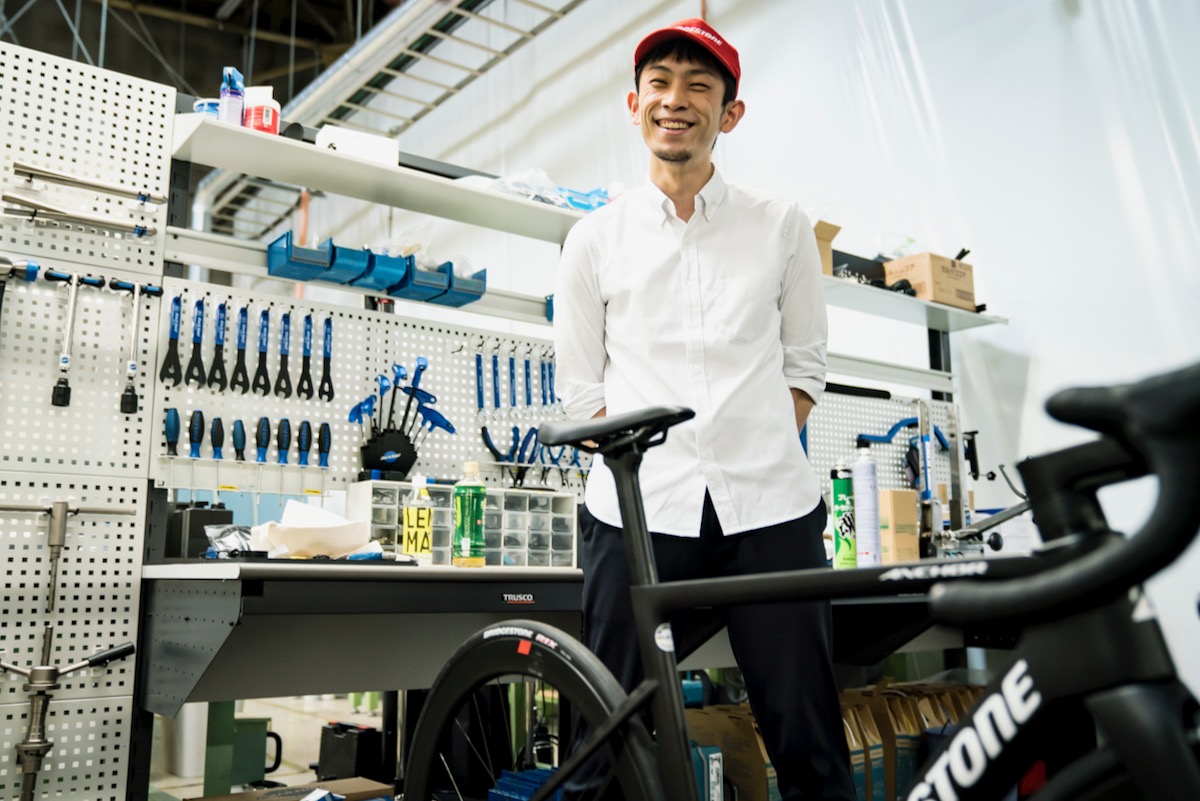
Q:「トラックバイクで培った剛性」と聞くと、どうしても硬い、とイメージしてしまうが振動吸収性はどうか?
硬くなることで振動吸収性がネガになることがありますが、既に実戦投入しているチームからも特に問題ないというフィードバックを受けています。エアロ効果を求めた形状でロードを作ると、どうしても縦方向に硬くなる傾向があるので、我々も気にしてはいたんですが、実用上問題ないレベルに仕上げられたと思っています。
Q:ロードレースに必要な剛性とは? どう硬く、どう柔らかくある必要があった?
選手が気にしていたのはやはりアタック時の反応でした。大きな出力で一気に踏んだ際にロスなく進むかどうかが重要だと考えています。またヘッド周りなどのハンドリングについても、下りなどでシビアに効いてくるポイントです。
Q:レース用ということだが、一般ユーザーが踏み負けてしまう、そんなことはない?
脚質次第だとは思いますが、比較的大きな出力で踏める選手向けに開発をしています。ですが、ほどほどの出力でもRP9の持つ気持ちよさは十分味わって頂けると思います。
社内の試乗でも「踏む気にさせられる」「速く走りたくなる」バイクだ、という声が出ています。踏んで気持ちいい、というのはロードバイクの楽しさの根源だと思っています。
レース出場のために日々練習を積み、週末を費やす選手のための現実的な一台
矢継ぎ早に質問と回答のやりとりをした結果、「世界を制した技術を使って作った、日本のレースで勝つためのロードバイク」というのが大きく印象に残った。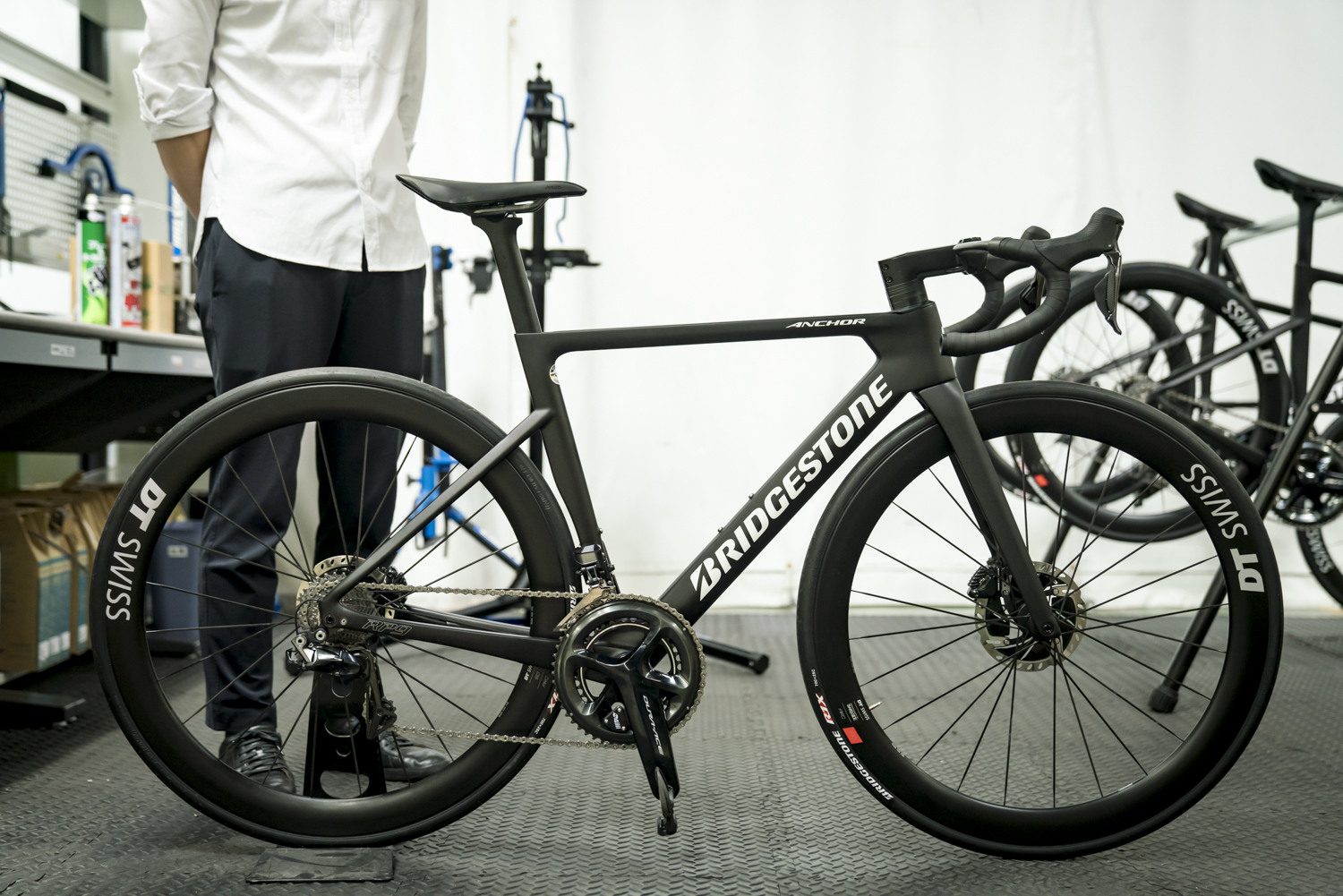
今後RP9に乗るライダーの多くは、例えば来月のレースで結果を残したい、と切に願う選手であるはずだ。実際に世界に挑戦できるのは、ほんのひと握りだろう。今目の前にいるひとりの日本の選手が、次のロードレースで勝てるように、と願ったバイク。そのために、綿密な計算と細かな調整を繰り返し作られたオールラウンダー。RP9はそのために作られた、という印象である。「世界を制した技術」を、単なるスローガンにしていない。
質疑応答が終わり、ここで藤野智一さんが口を開いた。元プロレーサーで、今はプロショップ「なるしまフレンド」に勤務する藤野さんには、このRP9を試乗してもらうため、この場に同行してもらっていたのだ。
「(まだテストしていない段階で)今良いな、と思えるのは価格ですよね。このスペックでフレームセット49万5千円(税込)は、だいぶコストを抑えてきた印象ですよね」。
さすが、実際にお客さんに接するショップからの視点である。この価格も、日本のブランドであるアンカーならではだと藤野さんは見抜く。性能、使い勝手、そして価格とすべてが現実的なのだ。RP9は日本のレースに勝てる性能を、レース出場のために日々練習を積み、週末を費やす選手が手にできるものに落とし込んでいる。
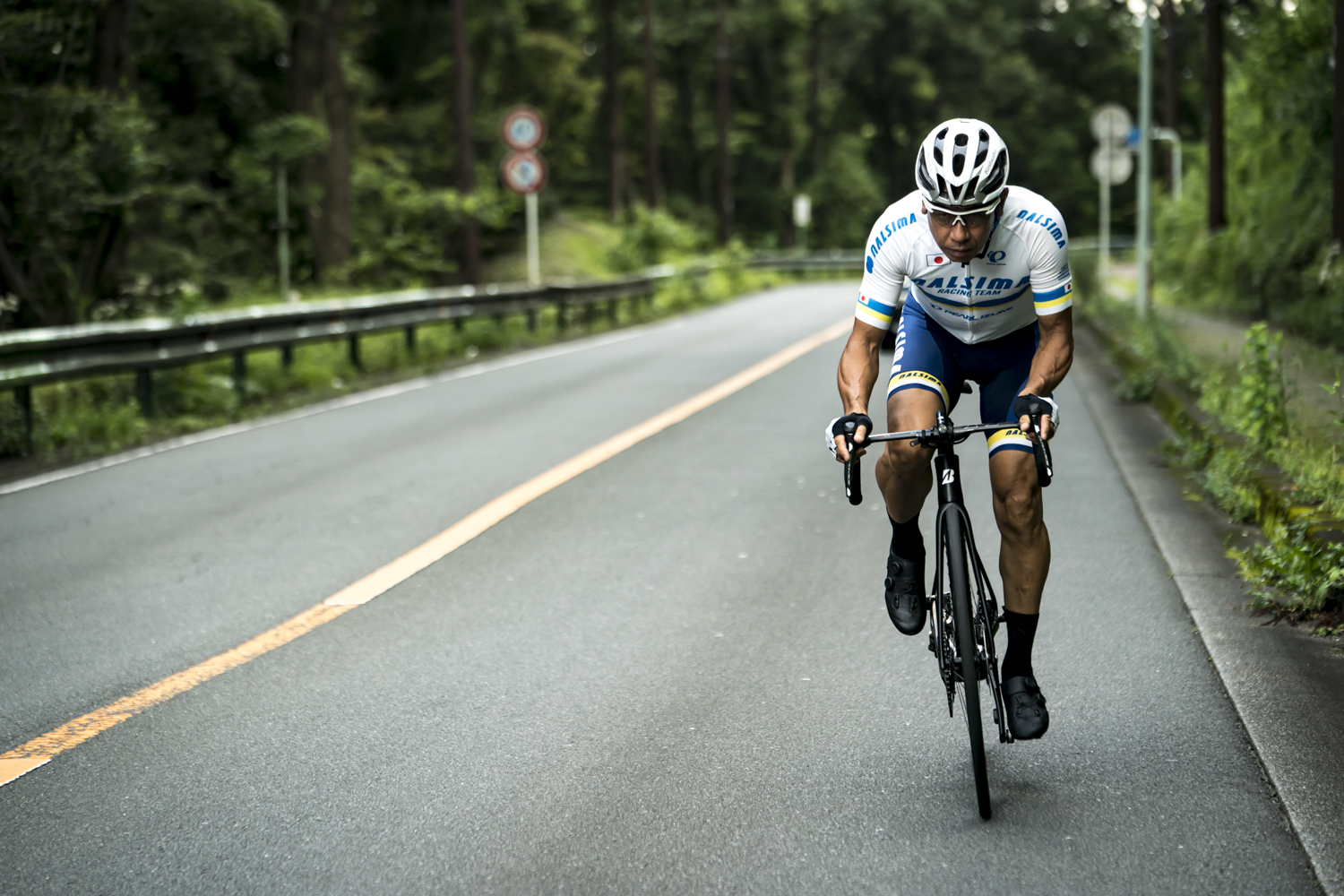
「使ってもらって、なんぼです」と中村さんは、言った。その通りである。次回は、藤野智一さんに、実際に使ってもらい、そのインプレを聞かせてもらう。
リンク
提供:ブリヂストンサイクル
text:Koichiro Nakamura/photo:Nobuhiko Tanabe
text:Koichiro Nakamura/photo:Nobuhiko Tanabe