以下に紹介するのは、ファクターでセールスマネージャーを務める元プロ選手、ジョン・エブセン氏に聞いたO2 V.A.M(以下VAM)についてのインタビュー。現在も世界トップレベルの登坂力を誇り、開発ライダーを務めた彼に、バイク内側に秘められたテクノロジーやその先進性をアピールしてもらった。
6月のMt.富士ヒルクライムに参戦したジョン・エブセン氏。現在でも超一級の登坂力を誇る photo:So.Isobe
デンマーク出身の元プロ選手。現在は台湾在住でファクターのセールスマネージャーを務める。2018年に引退するまでワンプロサイクリングやシンハーなどに在籍し、ワンプロ時代にファクターを使用していた。ヒルクライムを愛し、特に台湾KOMチャレンジには毎年参加して通算3勝するなど現在でも世界屈指の登坂力を誇る。ニックネームは"山岳サイボーグ"。VAMの開発ライダーも務め、カーボンに関しての知識も豊富。今回は自身が参加したMt.富士ヒルクライム会場でインタビューを聞いた。
その通り。形状こそO2譲りですが、中身は完全なる別物です。努力を重ねて世界トップのクライマーバイクに仕上がりました。VAMは54サイズの塗装済みフレームで約630gという類稀なる軽さを誇ります。他社では塗装無しの46サイズを計ったりとあらゆる手段を尽くしていますが、我々の数値はリアルです。おおよそ1サイズ上がると30g増加し、1サイズ下がれば15gほど軽くなります。
「O2 V.A.Mは現在最も進化したハイテククライマーバイク」 (c)Factor Bikes
「VAMは通常の2倍以上の時間を掛けて設計を行いました」 photo:So.IsobeVAMを特別な存在たらしめるのは、我々が新しく投入した製法技術と素材にあります。製法に関して詳しくは企業秘密ですが、一般的なカーボンフレームは成型段階でフレーム内部にプラスチック製のプラダーを使うところ、VAMは従来無いラテックス製のスタイロフォームを使うことでフレーム内部を滑らかに保ち、カーボンの使用量を極限まで抑えることに成功しています。
フレーム内部を完全にクリーンな状態にすることで、例えばブレーキラインやケーブル、ワイヤーなどを組む際にもトラブルは生じません。ほとんどの一般ユーザーはカーボンフレームの内側を見たことがないと思いますが、カーボンバイクの大多数はBBやシートチューブ内側に余分なカーボン積層が残されており、これが重量や剛性のバラつき、そして内装ワイヤー/ケーブルを組む際のトラブルに繋がります。しかしながらこの部分に気を配っているカーボン工場は多くありません。
それに加え、VAMはフレーム全体が2ピース構造であることも重量を削減するポイント。前三角と後ろ三角を別々に成型して接着しているのですが、一般的なフレームの場合5ピースを接着で繋げます。接着数が少ないほど軽く強いフレームができるとは簡単に想像できるでしょう?それには各サイズごとに金型が必要になるのでコストが必要ですが、我々は自社製造できるメリットがあります。
― カーボン素材に関しては?
VAMには最先端素材であるテキストリームカーボンとピッチ系カーボンファイバーを多く奢り、一般的に使われるT800やT1000といったカーボンはほぼ使いません。これら素材は扱いが非常に難しいので、開発を外部委託しているブランドでは本来の性能を出し切れないことがほとんどです。
例えばC社、F社、B社、C社など世界の一流ブランドのOEM生産を請け負う自社工場を保有しているので、技術としては世界屈指です。
開発でも他社とは比較にならないくらい妥協なく、時間をかけて性能を追求することができますし、開発費が抑えられることはつまり、販売価格を抑えることにも繋がります。実際にVAMは一般的なロードバイクの2倍以上の開発期間をかけましたが、他社では通常10万円ほどするブラックインクの一体式ハンドルや、シートポスト、セラミックスピード製BB、その他バーテープといった小物類を付属させながらフレームセット値段は60万円に抑えているので、実質的なフレーム価格はずっとリーズナブル。そうそう、もちろん他社の技術流用をしていないこともメンションしておきます。
「フレーム内側にこそ高性能カーボンを使用すべき」 (c)Factor Bikes
ファクターオーナーのロブ・ギティス氏。台湾のスポーツサイクリング産業に深く関わる人物だ (c)Factor Bikes
2019年12月には、かつてサーヴェロなどトップブランドで活躍したエンジニア、グラハム・シュライブ氏を迎えることが発表された (c)Factor Bikes
性能を第一にする一つの例として、先ほど取り上げたテキストリームカーボンを例にとりましょう。大きな織り目が目立つカーボンシートですが、VAMのフレームでその目地が見えることはありません。これはなぜでしょう?答えは、テキストリームはフレーム表面に使ってもあまり意味がないからです。我々の研究では、剛性が必要なフレーム内側に配置してこそ最大限効果を発揮するものなので、VAMではBB周り、そしてヘッドチューブなど負荷のかかる場所に集中的に使っています。ただ軽いフレームを作るのは簡単ですが、トップライダーを満足させる走りも叶えるのは並大抵の技術では叶わないことなのです。
― なるほど。あなたはVAMのテスターを務めたと聞きましたが、今回の富士ヒルクライムで乗っていたのは完成版ですか?
今回持ってきたのは最終盤のプロトタイプ。細部の細かい仕様が製品版とは異なりますが、カーボンに関しては全く一緒です。開発中はプロトタイプを作ってはテストを行い、その数は1年で15本を超えました。1ヶ月ごとにバイクを乗り換えて、そのフィードバックを開発チームに伝えました。
Mt.富士ヒルクライムではリムブレーキ版のVAMを使用した photo:So.Isobe
Mt.富士ヒルクライムでアタックを繰り返す photo:Naoki.Yasuoka
「セットのブラックインク製一体ハンドルとシートポストを使ったまま5.98kgを達成」 photo:So.Isobe
そうして生まれた完成版には一切の妥協がありません。クライマーの私はリムブレーキ版に乗っていますが、重量が軽いことに加え、剛性も確保されているのでとにかく瞬発力が高い。軽く硬いだけのフレームはここまでですが、BB周辺のしなりも計算に入れているため踏みやすく、平地巡航も得意です。リムブレーキ版もO2と異なりダイレクトマウントを取り入れ、かつブレーキ台座周辺を強化しているので、ドライコンディションでの制動力はディスクブレーキに引けを取りません。軽さを優先するならリム版を、バイクのトータル性能を底上げするならディスク版と、ユーザーの好みで選べるのは良い部分だと感じています。
イスラエルサイクリングアカデミーのチームカラーに塗られたVAM。その活躍が楽しみだ (c)Factor Bikes
完成版のVAMはディスクブレーキにチューブラータイヤの組み合わせで6.4kg。台湾のプロショップが軽量ホイールに交換したら、セットのブラックインク製一体ハンドルとシートポストを使ったまま5.98kgを達成できました。UCIレースで使う場合は重りを積まないといけませんが、ホビーレースやヒルクライムであればその軽さを最大限活かすことができます。
これだけの性能を有していながら価格は各社のハイエンドモデルと比べてリーズナブルであることは大きな武器ですね。我々の技術の粋を集めたVAMは、現時点世界で最も進んだハイテクノロジーバイクだと言えます。日本はヒルクライムレースが盛んですし、VAMがフィットするユーザーは少なくないと確信しています。
ジョン・エブセン氏 プロフィール

デンマーク出身の元プロ選手。現在は台湾在住でファクターのセールスマネージャーを務める。2018年に引退するまでワンプロサイクリングやシンハーなどに在籍し、ワンプロ時代にファクターを使用していた。ヒルクライムを愛し、特に台湾KOMチャレンジには毎年参加して通算3勝するなど現在でも世界屈指の登坂力を誇る。ニックネームは"山岳サイボーグ"。VAMの開発ライダーも務め、カーボンに関しての知識も豊富。今回は自身が参加したMt.富士ヒルクライム会場でインタビューを聞いた。
「現在最も進化したハイテククライマーバイク」
― 今日はよろしくお願いします。パッと見はO2とそこまで大きな差はありませんが、実際には大きな進化を果たしていると聞きました。その通り。形状こそO2譲りですが、中身は完全なる別物です。努力を重ねて世界トップのクライマーバイクに仕上がりました。VAMは54サイズの塗装済みフレームで約630gという類稀なる軽さを誇ります。他社では塗装無しの46サイズを計ったりとあらゆる手段を尽くしていますが、我々の数値はリアルです。おおよそ1サイズ上がると30g増加し、1サイズ下がれば15gほど軽くなります。
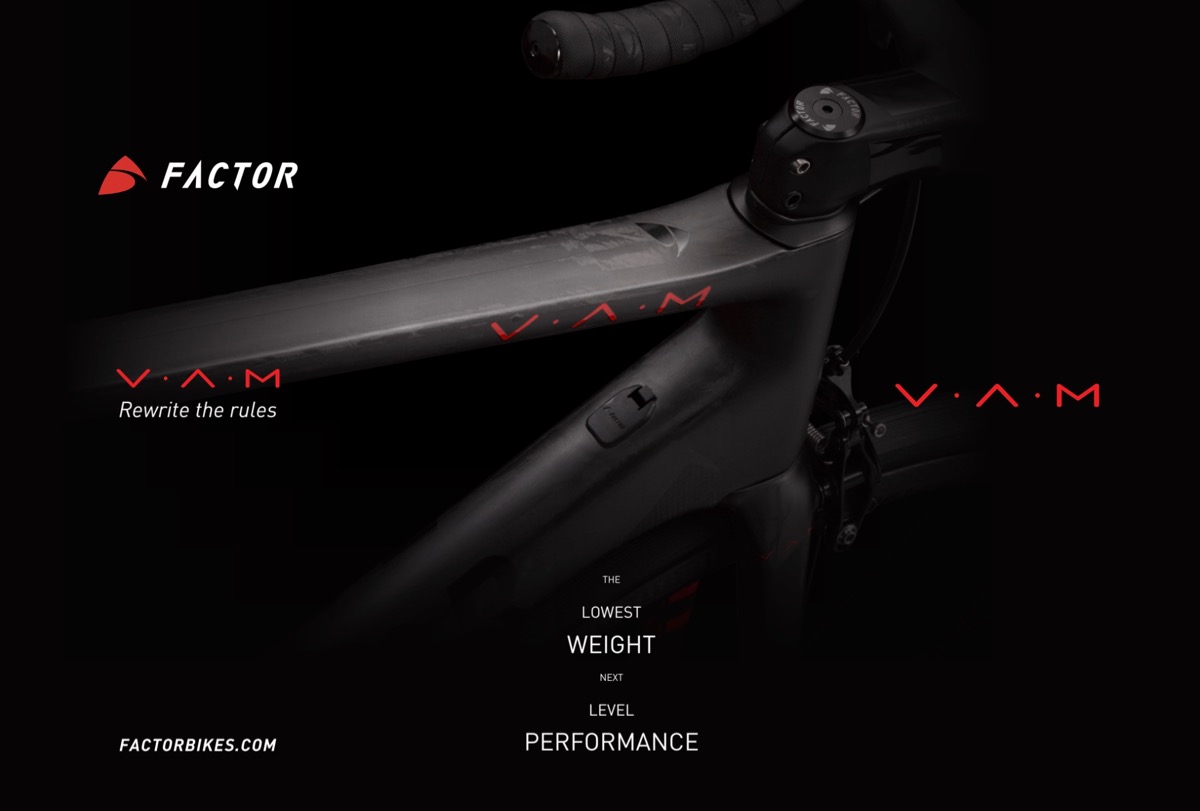
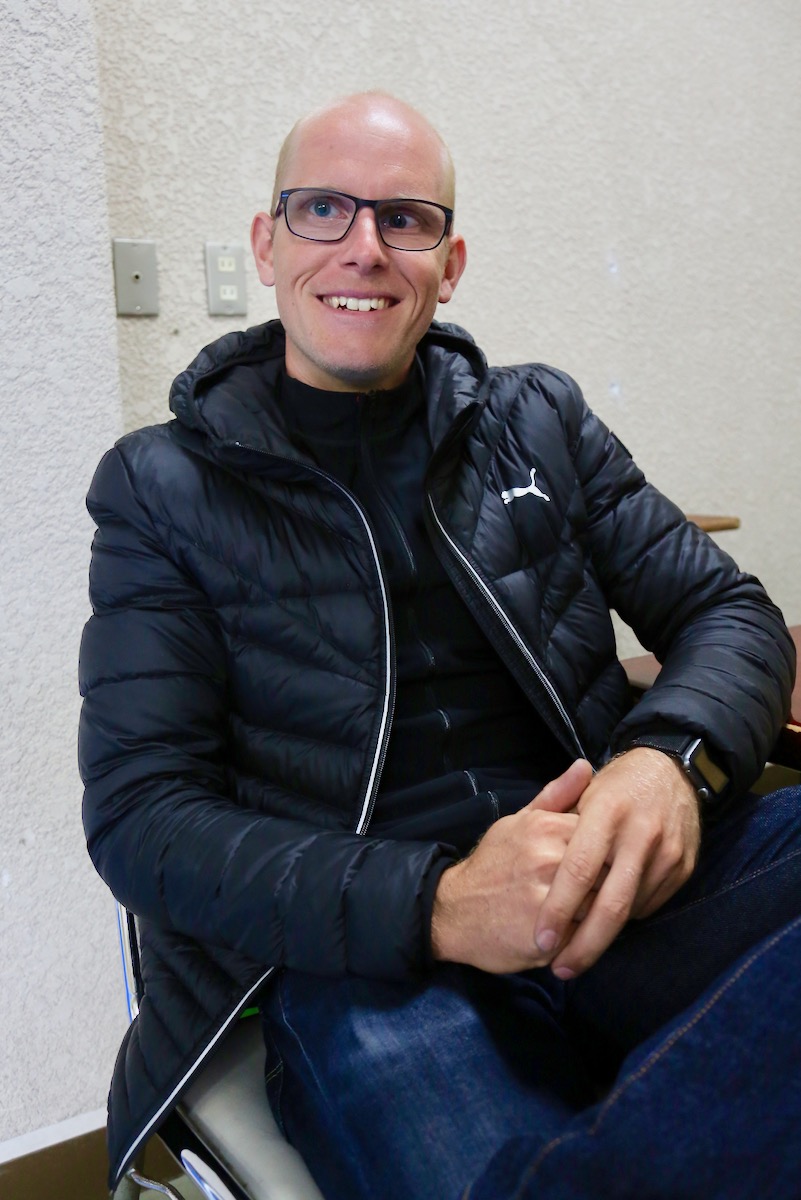
フレーム内部を完全にクリーンな状態にすることで、例えばブレーキラインやケーブル、ワイヤーなどを組む際にもトラブルは生じません。ほとんどの一般ユーザーはカーボンフレームの内側を見たことがないと思いますが、カーボンバイクの大多数はBBやシートチューブ内側に余分なカーボン積層が残されており、これが重量や剛性のバラつき、そして内装ワイヤー/ケーブルを組む際のトラブルに繋がります。しかしながらこの部分に気を配っているカーボン工場は多くありません。
それに加え、VAMはフレーム全体が2ピース構造であることも重量を削減するポイント。前三角と後ろ三角を別々に成型して接着しているのですが、一般的なフレームの場合5ピースを接着で繋げます。接着数が少ないほど軽く強いフレームができるとは簡単に想像できるでしょう?それには各サイズごとに金型が必要になるのでコストが必要ですが、我々は自社製造できるメリットがあります。
― カーボン素材に関しては?
VAMには最先端素材であるテキストリームカーボンとピッチ系カーボンファイバーを多く奢り、一般的に使われるT800やT1000といったカーボンはほぼ使いません。これら素材は扱いが非常に難しいので、開発を外部委託しているブランドでは本来の性能を出し切れないことがほとんどです。
「自社開発・生産できることは大きなメリット」
― 自社工場では他ブランドのOEM生産も請け負っていると聞きました。例えばC社、F社、B社、C社など世界の一流ブランドのOEM生産を請け負う自社工場を保有しているので、技術としては世界屈指です。
開発でも他社とは比較にならないくらい妥協なく、時間をかけて性能を追求することができますし、開発費が抑えられることはつまり、販売価格を抑えることにも繋がります。実際にVAMは一般的なロードバイクの2倍以上の開発期間をかけましたが、他社では通常10万円ほどするブラックインクの一体式ハンドルや、シートポスト、セラミックスピード製BB、その他バーテープといった小物類を付属させながらフレームセット値段は60万円に抑えているので、実質的なフレーム価格はずっとリーズナブル。そうそう、もちろん他社の技術流用をしていないこともメンションしておきます。
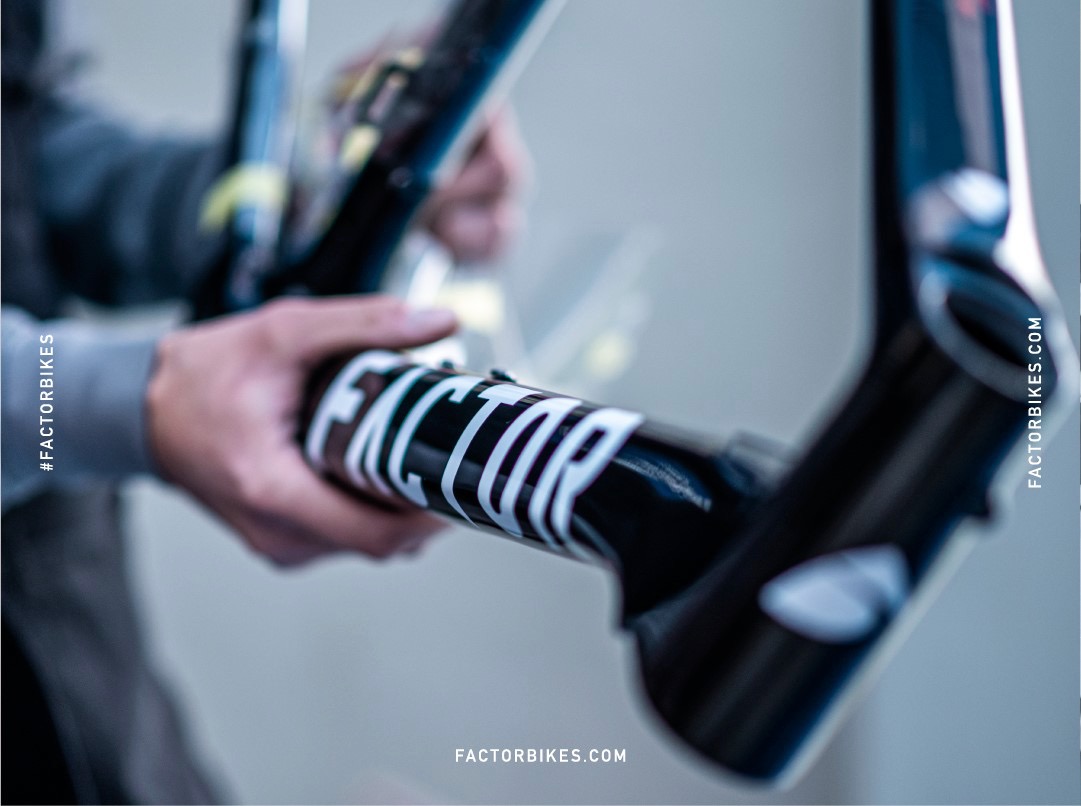
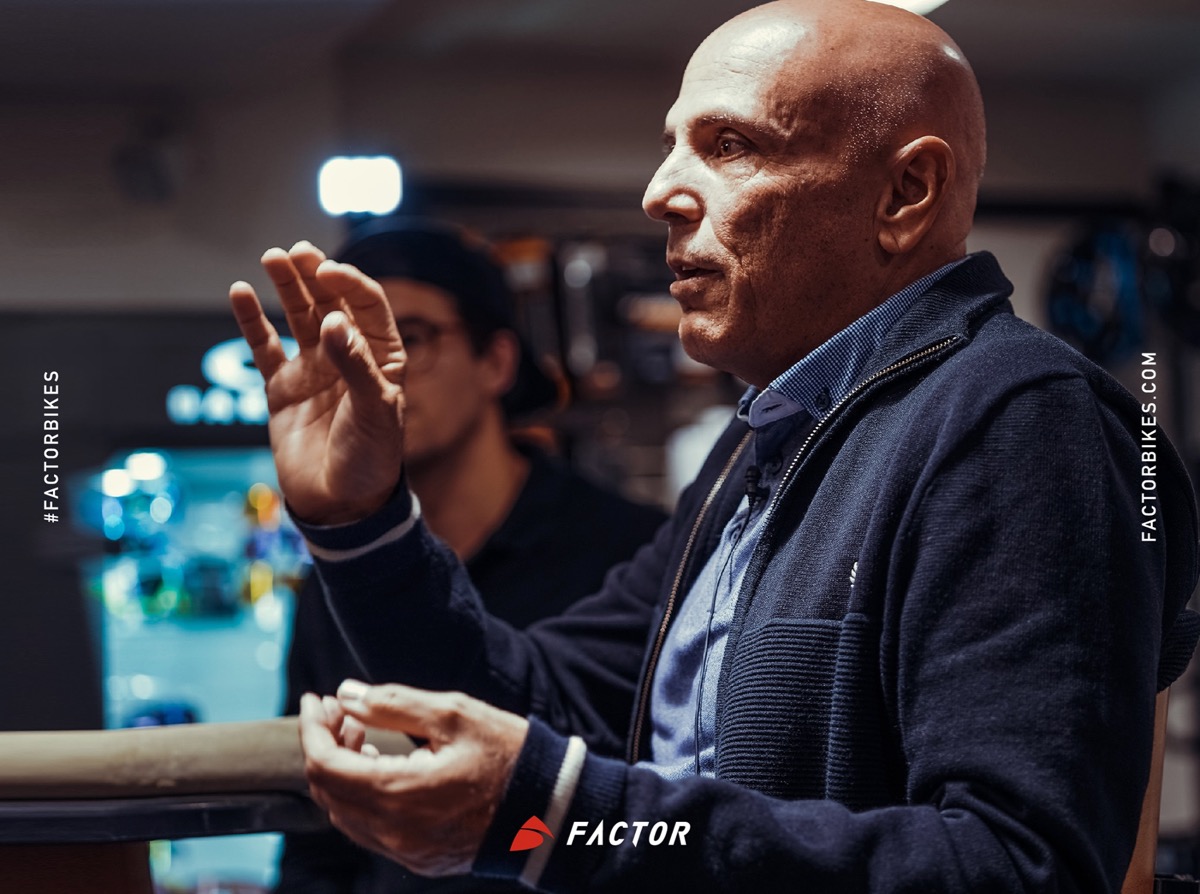
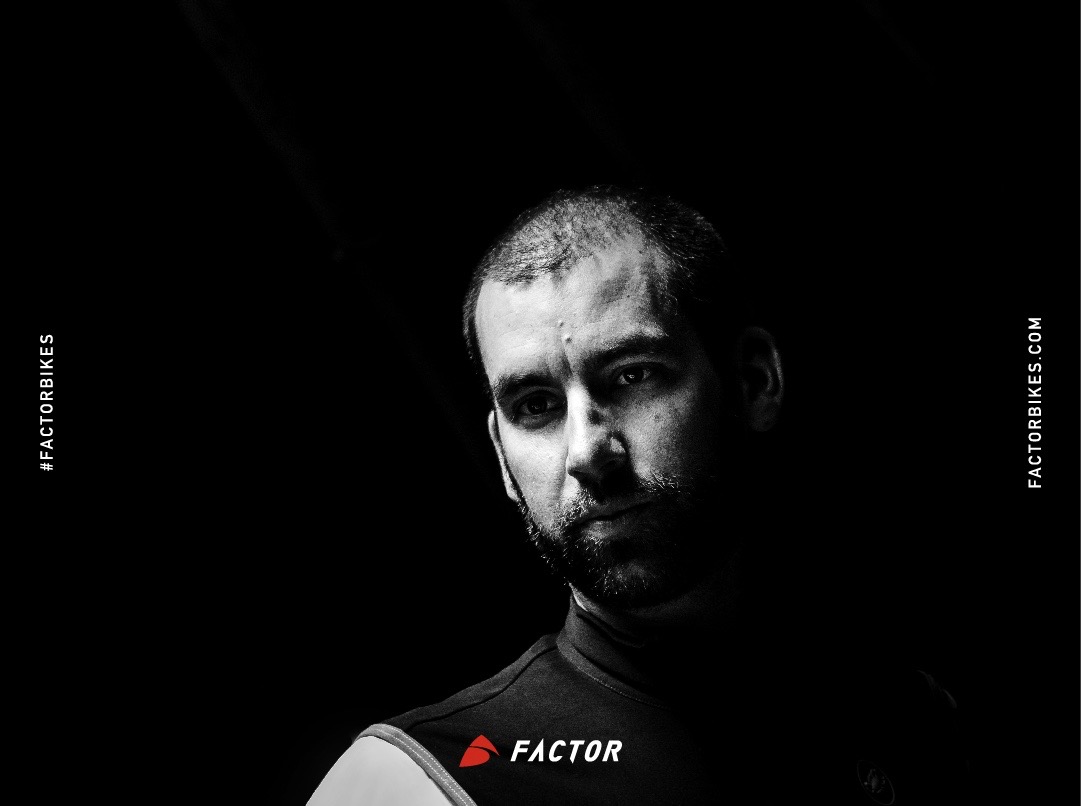
性能を第一にする一つの例として、先ほど取り上げたテキストリームカーボンを例にとりましょう。大きな織り目が目立つカーボンシートですが、VAMのフレームでその目地が見えることはありません。これはなぜでしょう?答えは、テキストリームはフレーム表面に使ってもあまり意味がないからです。我々の研究では、剛性が必要なフレーム内側に配置してこそ最大限効果を発揮するものなので、VAMではBB周り、そしてヘッドチューブなど負荷のかかる場所に集中的に使っています。ただ軽いフレームを作るのは簡単ですが、トップライダーを満足させる走りも叶えるのは並大抵の技術では叶わないことなのです。
― なるほど。あなたはVAMのテスターを務めたと聞きましたが、今回の富士ヒルクライムで乗っていたのは完成版ですか?
今回持ってきたのは最終盤のプロトタイプ。細部の細かい仕様が製品版とは異なりますが、カーボンに関しては全く一緒です。開発中はプロトタイプを作ってはテストを行い、その数は1年で15本を超えました。1ヶ月ごとにバイクを乗り換えて、そのフィードバックを開発チームに伝えました。
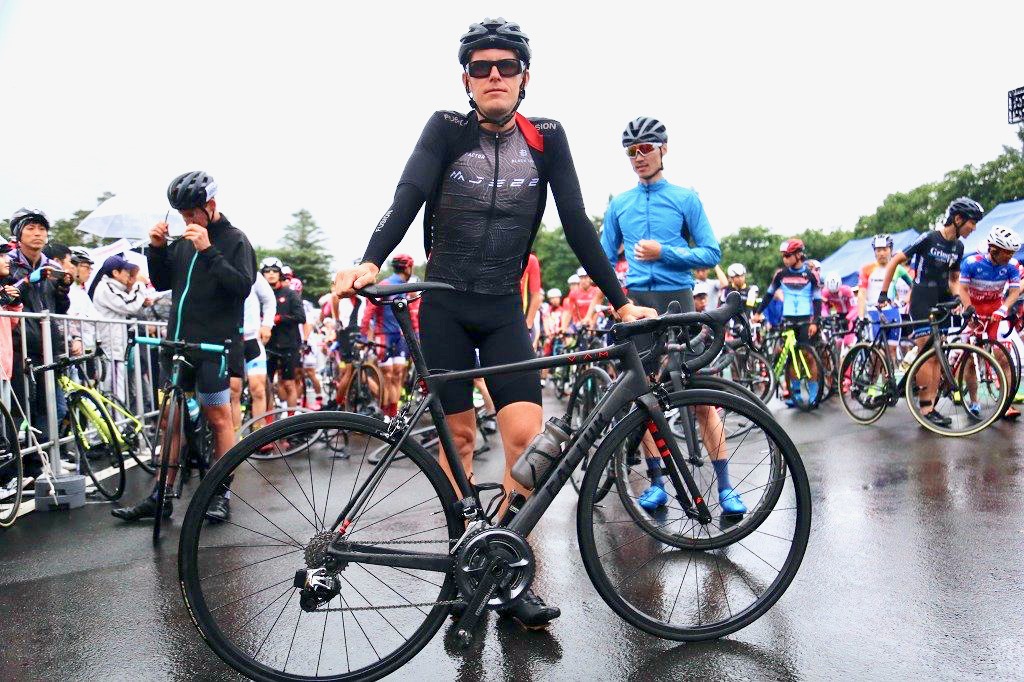
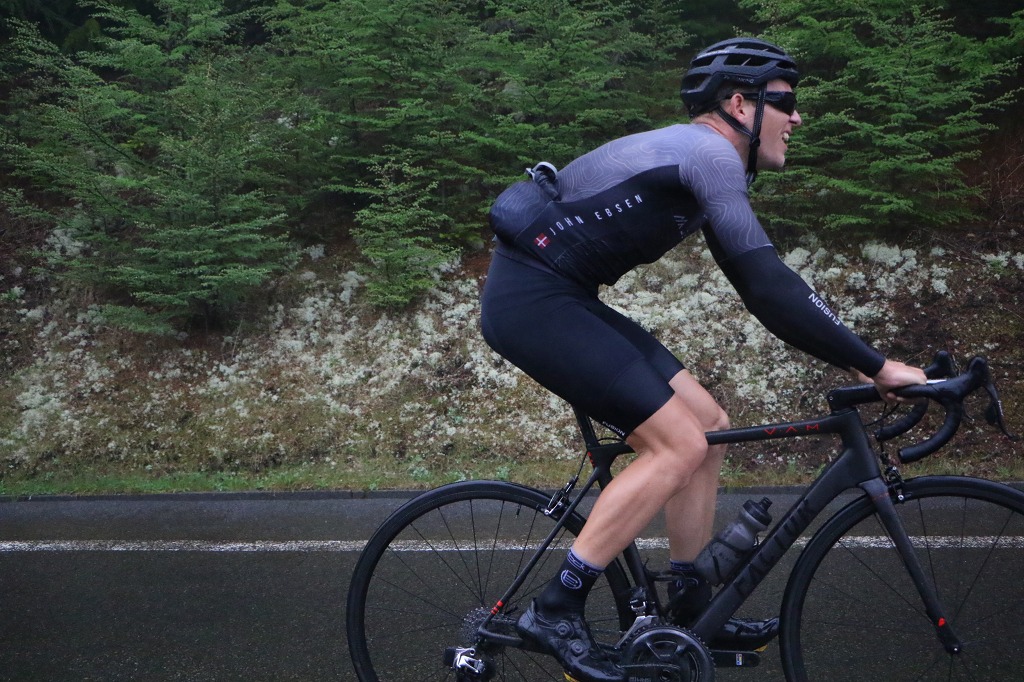
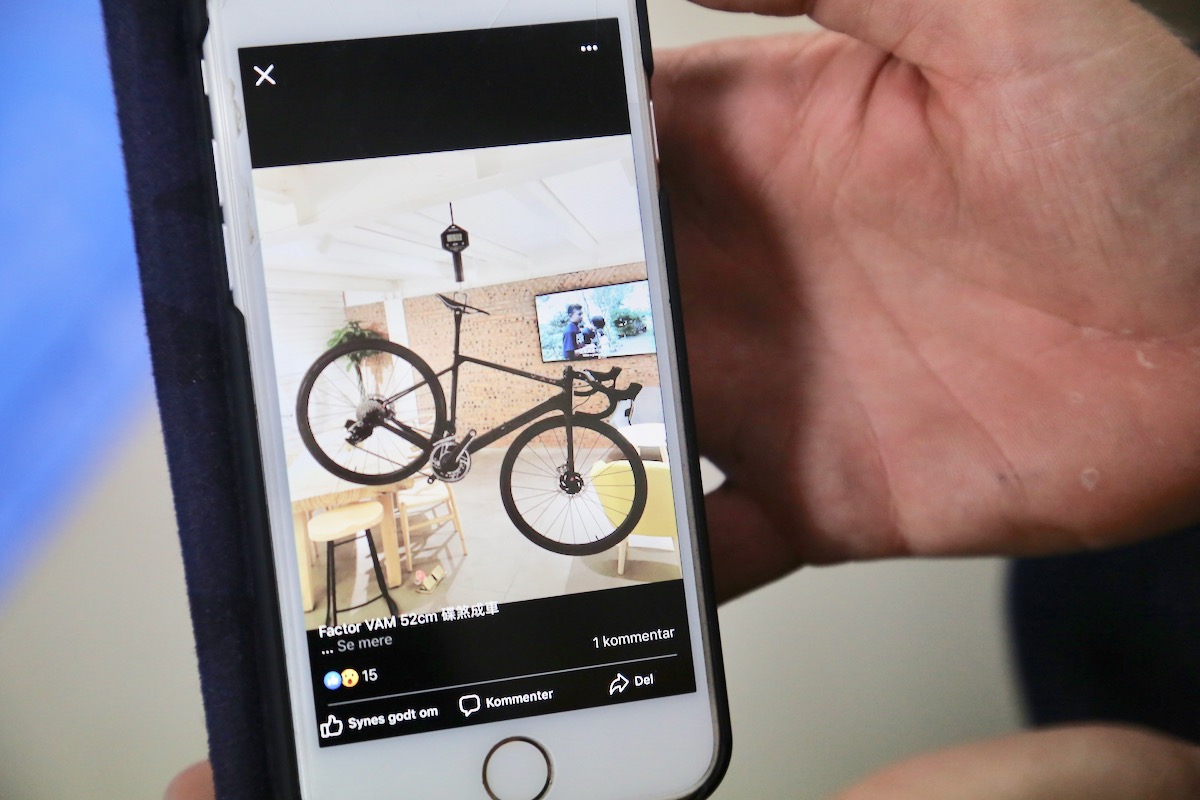
そうして生まれた完成版には一切の妥協がありません。クライマーの私はリムブレーキ版に乗っていますが、重量が軽いことに加え、剛性も確保されているのでとにかく瞬発力が高い。軽く硬いだけのフレームはここまでですが、BB周辺のしなりも計算に入れているため踏みやすく、平地巡航も得意です。リムブレーキ版もO2と異なりダイレクトマウントを取り入れ、かつブレーキ台座周辺を強化しているので、ドライコンディションでの制動力はディスクブレーキに引けを取りません。軽さを優先するならリム版を、バイクのトータル性能を底上げするならディスク版と、ユーザーの好みで選べるのは良い部分だと感じています。
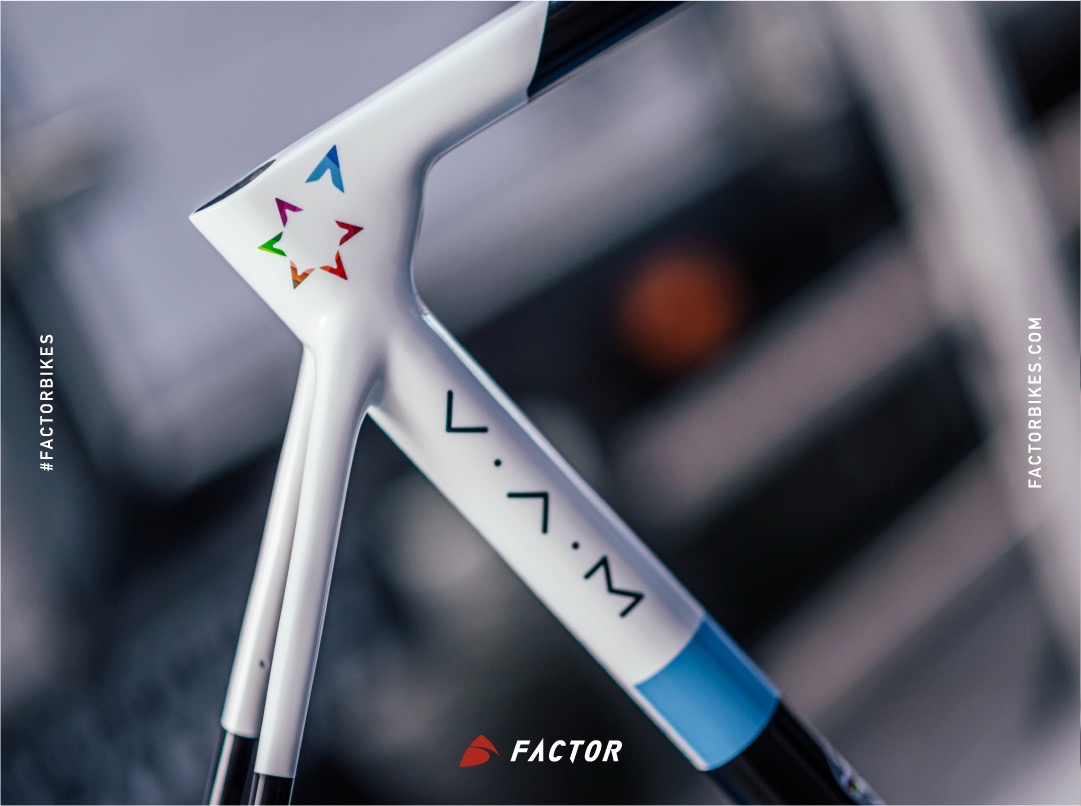
完成版のVAMはディスクブレーキにチューブラータイヤの組み合わせで6.4kg。台湾のプロショップが軽量ホイールに交換したら、セットのブラックインク製一体ハンドルとシートポストを使ったまま5.98kgを達成できました。UCIレースで使う場合は重りを積まないといけませんが、ホビーレースやヒルクライムであればその軽さを最大限活かすことができます。
これだけの性能を有していながら価格は各社のハイエンドモデルと比べてリーズナブルであることは大きな武器ですね。我々の技術の粋を集めたVAMは、現時点世界で最も進んだハイテクノロジーバイクだと言えます。日本はヒルクライムレースが盛んですし、VAMがフィットするユーザーは少なくないと確信しています。
提供:トライスポーツ、制作:シクロワイアード編集部