スイス国内の専用自社工場において、フルオートメーション化された機械によって生み出される逸品“impec(インペック)”が発表された。カーボンフレーム製作の新たな挑戦を始めた「BMC」が放つ、オンリーワンの存在感を持つこのモデルを、プレゼンテーションやインプレッションの様子を交えて紹介していこう。
BMC本社近くに建設されたカーボンフレーム製造専門のファクトリー photo:BMC
1994年にスイスで誕生した“BMC”。独自の最先端技術によって数々の名車を生み出し、ロードバイクからMTB、クロスバイクをリリースする総合ブランドとして世界的な成長を遂げた。2008年からはBMCレーシングチームを展開。同チームには現世界チャンピオンのカデル・エヴァンス(オーストラリア)も在籍し、ツール・ド・フランスやジロ・デ・イタリアなどのビックレースで活躍するビッグチームの一つに数えられている。
2010年、本拠地であるスイス中部のグレンヒェンにカーボン製造工場を完成。完全スイスメイドの革新的なフレーム製造をスタートさせた。
BMC本社に誇らしげに飾られたアメリカチャンピオンジャージとアルカンシェル photo:Kei Tsuji
Hand Made by Machinesをコンセプトに、フルオートメーションを実現したカーボンフレーム製造専門のファクトリー photo:BMC
「スイス」という国名は、それだけで一つのブランドであると言える。時計しかり。ナイフ類しかり。
スイスと聞けば、職人の手によって生み出される高性能で精密な高級工業製品を思い浮かべる人も多いだろう。その美しき製品の数々は多くの人々を魅了し、この国から数々の名品が生み出されてきた。BMCの本社近くには、スイスを代表する名立たる時計メーカーが拠点を構えている。古くからその一帯は精密工業のメッカとして世界的な地位を築いてきた。
そして2011年――1台のロードバイクが誕生した。
ついにベールを脱いだBMCの秘密兵器 impec photo:BMC
impecのフレーム製造は、まず「スターゲイト」と名付けられた巨大なカーボン編み機から、筒状に編み込まれたシームレス(継ぎ目のない)カーボンチューブが編み出されるところから始まる。3メートルほどもある機械外周を128本のボビンが複雑に回転しながらカーボンチューブを編み出して行く様は圧巻だ(LSW)。
「スターゲイト」と名付けられた巨大なカーボン編み機。由来は米国のSF映画&TVドラマシリーズのタイトルおよび星間移動装置の形状から photo:BMC
シームレス製作技法は一部の他メーカーで既に採用されていたが、BMCの機械の大きさは桁違いで、編み出しと同時に形状を決め、成型へと移行する。カーボンの編み込みからパイプの完成まで、フルオートメーションの機械がそれぞれ分担し、その間に人の手は入らない。そのため一切のムラの無い状態でカーボンパイプとして完成させることができる。
またimpecではモノコックではなく、カーボン+サーモプラスチックを使用したインジェクション成型ラグを用いてフレームを形作っているが、このラグも驚くべき高精度で製造されている(SNC)。
しかし、最も驚くべきはここまで徹底した機械化を行いながらも、その目的が大量生産による製造コストの低減などではないということだ。シームレスチューブは一本ずつしか製造できず、成型後のラグを光学検査までする「完璧」を追い求めた結果が、最先端の工業製造ラインを新たに建設するというこだわりをみせる。
海外ではなく、スイス本国に製造拠点を建造したのは、情熱を持ったBMCスタッフによる手と心が作り出す「完璧」を追求した結果だと言える。「Hand Made by Machines(マシンによるハンドメイド)」というキャッチがこれほど似合う工場は他に無いだろう。
ラグの接着を行なうロボット ブルーのライトがラグを照らし、カメラで接着剤の量を確認する photo:BMC
大型ロボットの導入によりフルオートメーションを実現 photo:BMC
「完璧」を追求し、マシンによるハンドメイド、という解を得て紡ぎ出されたフレームがimpecだ photo:BMC
LSW 継ぎ目なく編み込まれたカーボンの筒を成型 photo:BMC
通常、カーボンフレームはカーボンシートを積層させて製造することになるのだが、この方法では部位ごとのバラつきが出て、継ぎ目の強度確保が必要となる。しかし、impecに採用されたLSW(Load Specific Weave)製法は、継ぎ目なく編み込まれたカーボンの筒を成型して製造するため、繊維の密度を変えることで、さまざまな特性を持たせることが可能となる。
例えば、「曲がる」と「ネジれる」といった違った方向に掛る力に対する剛性も、一本のチューブ内に持たせることができ、フレーム各部ごとに最適な特性を引き出すことができる。また、すべての工程が機械によるフルオートメーション化されたことで、製造されるすべてのフレームは高い品質を保持することが可能となっている。
LSW製法によって編み込まれた状態のカーボンの筒 photo:Kei Tsuji
LSW製法によって作り出されたimpecのトップチューブは断面が六角形 photo:Kei Tsuji
SNC サーモプラスチィックとカーボンを用いてインジェクション成型される photo:BMCimpecに投入されたもう一つの最新製造技術が、SNC(shell node concept)。サーモプラスチィックとカーボンを用いてインジェクション(注入)成型して作られたシェルで、カーボンパイプを挟み込む方法だ。
impecではLSWで製造されたシームレスパイプの特性を活かすために、パイプをシェルでつなぐという方法を採用。重量的にはシェル部分が加わることで、昨年のトップモデル“teammachine SLR01”よりやや重量増になったが、この製法によってより完璧な精度を実現している。また、右左のシェルはオス・メスに分かれていて、しっかりと両側からパイプをつかむように設計。さらに、すべてのシェルは光学検査された後、特殊な接着剤を使用して接合される。
SNC製法によって作られた高精度シェル photo:Kei Tsuji
高精度シェルが寸分の狂い無くチューブを包み込む photo:Kei Tsuji
次のページではBMC本社にて行われたプレゼンテーションの模様を通じてimpecのテクノロジーとスペックを紹介する。
本国スイスに自社工場が完成! バイクブランド「BMC」
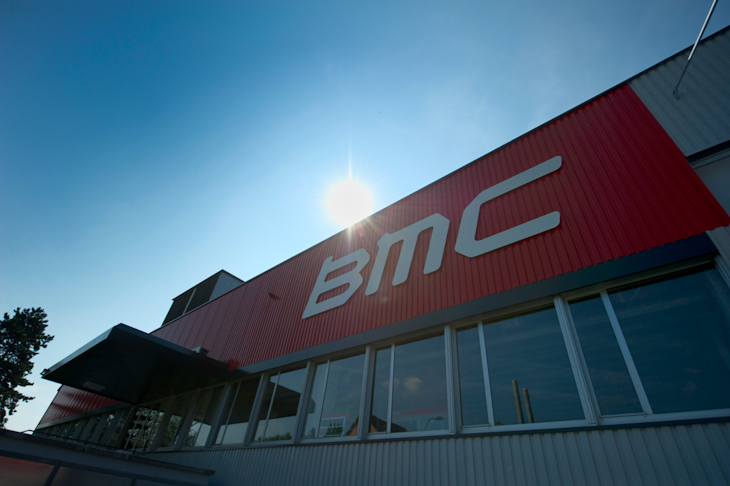
1994年にスイスで誕生した“BMC”。独自の最先端技術によって数々の名車を生み出し、ロードバイクからMTB、クロスバイクをリリースする総合ブランドとして世界的な成長を遂げた。2008年からはBMCレーシングチームを展開。同チームには現世界チャンピオンのカデル・エヴァンス(オーストラリア)も在籍し、ツール・ド・フランスやジロ・デ・イタリアなどのビックレースで活躍するビッグチームの一つに数えられている。
2010年、本拠地であるスイス中部のグレンヒェンにカーボン製造工場を完成。完全スイスメイドの革新的なフレーム製造をスタートさせた。
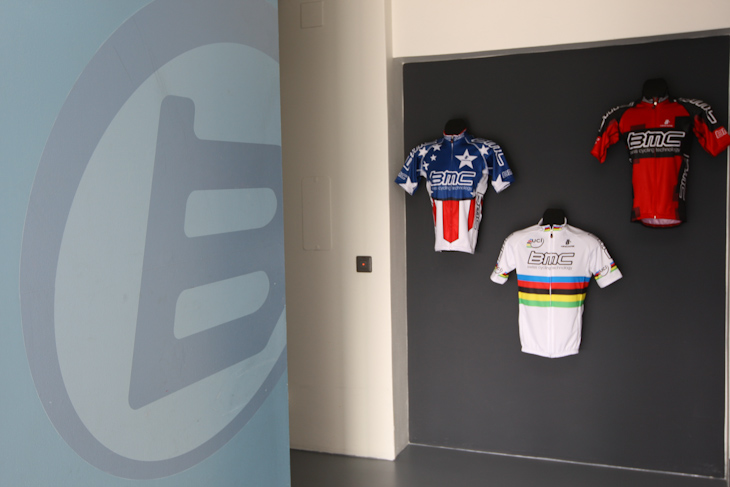
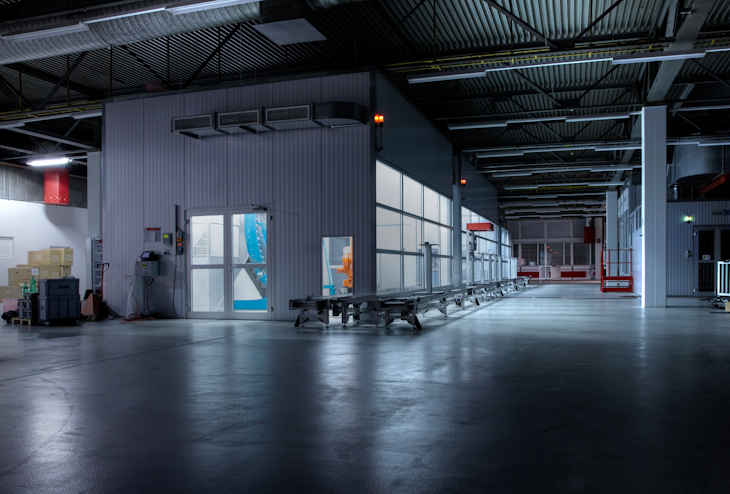
「スイス」という国名は、それだけで一つのブランドであると言える。時計しかり。ナイフ類しかり。
スイスと聞けば、職人の手によって生み出される高性能で精密な高級工業製品を思い浮かべる人も多いだろう。その美しき製品の数々は多くの人々を魅了し、この国から数々の名品が生み出されてきた。BMCの本社近くには、スイスを代表する名立たる時計メーカーが拠点を構えている。古くからその一帯は精密工業のメッカとして世界的な地位を築いてきた。
そして2011年――1台のロードバイクが誕生した。
“BMC impec”
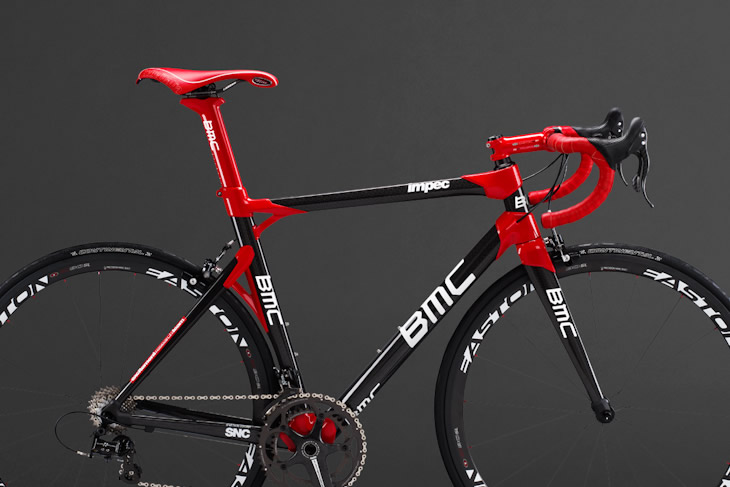
impecのフレーム製造は、まず「スターゲイト」と名付けられた巨大なカーボン編み機から、筒状に編み込まれたシームレス(継ぎ目のない)カーボンチューブが編み出されるところから始まる。3メートルほどもある機械外周を128本のボビンが複雑に回転しながらカーボンチューブを編み出して行く様は圧巻だ(LSW)。
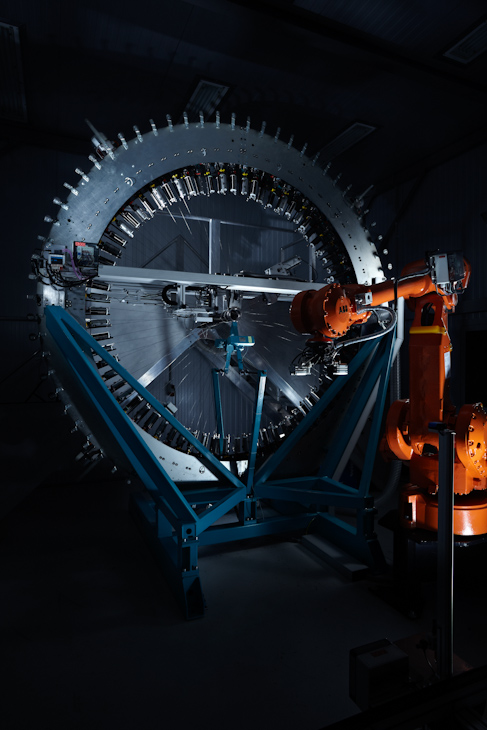
またimpecではモノコックではなく、カーボン+サーモプラスチックを使用したインジェクション成型ラグを用いてフレームを形作っているが、このラグも驚くべき高精度で製造されている(SNC)。
しかし、最も驚くべきはここまで徹底した機械化を行いながらも、その目的が大量生産による製造コストの低減などではないということだ。シームレスチューブは一本ずつしか製造できず、成型後のラグを光学検査までする「完璧」を追い求めた結果が、最先端の工業製造ラインを新たに建設するというこだわりをみせる。
海外ではなく、スイス本国に製造拠点を建造したのは、情熱を持ったBMCスタッフによる手と心が作り出す「完璧」を追求した結果だと言える。「Hand Made by Machines(マシンによるハンドメイド)」というキャッチがこれほど似合う工場は他に無いだろう。
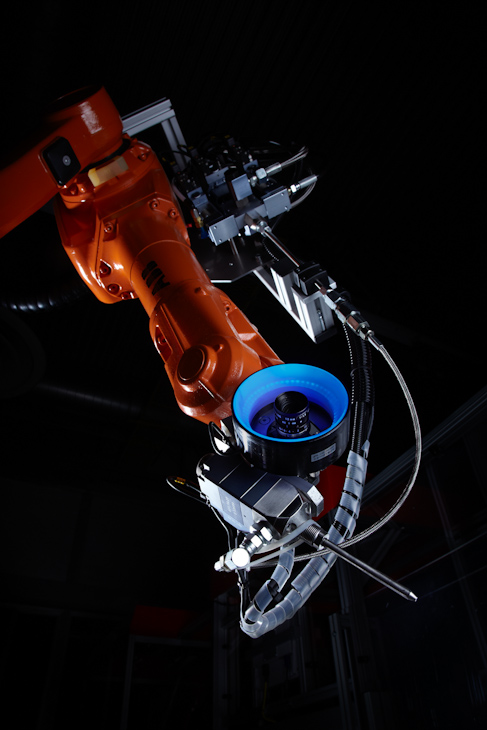
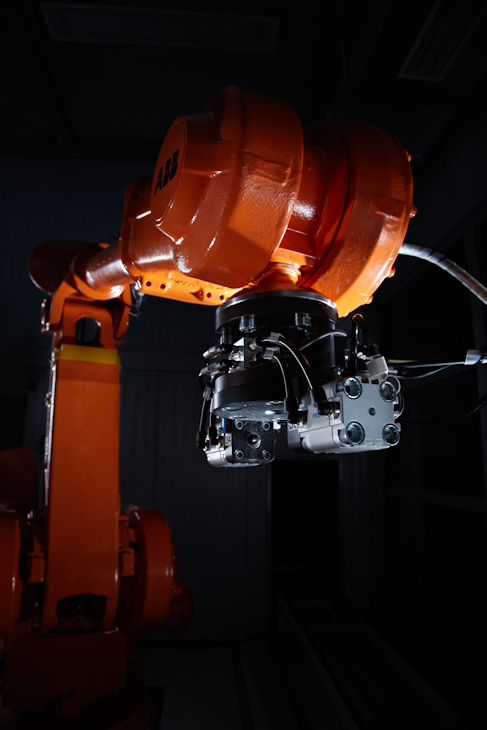
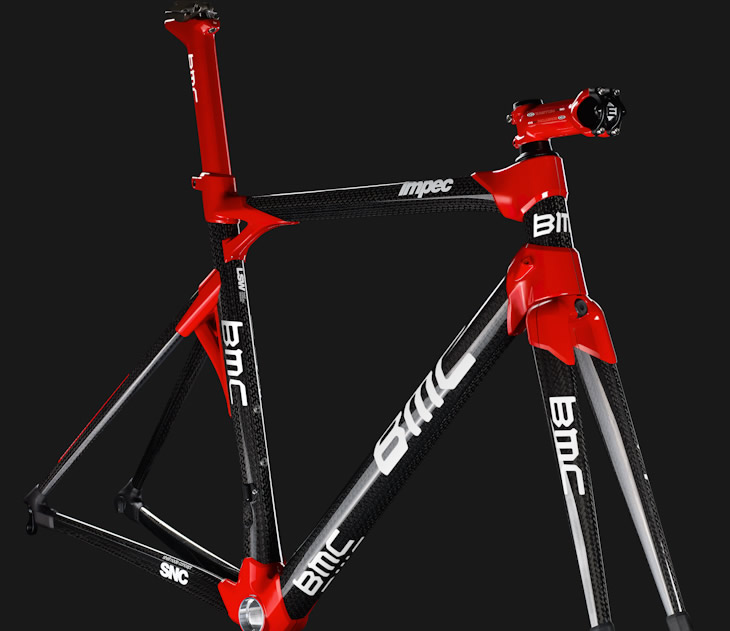
フルオートメーションによるハンドメイドの実力
LSW
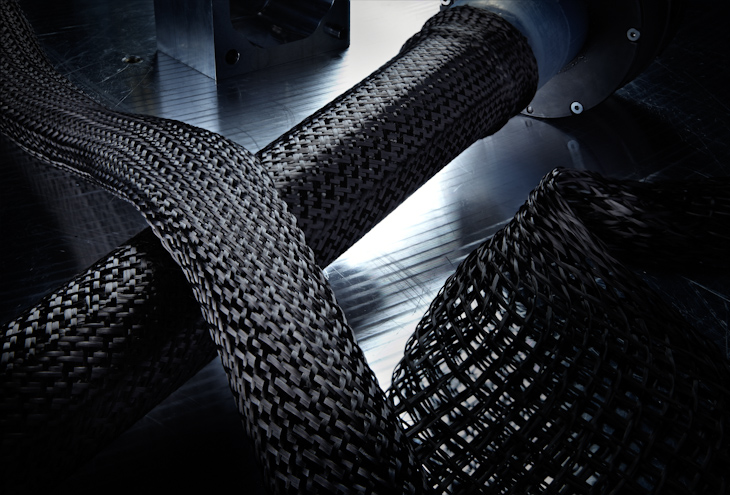
例えば、「曲がる」と「ネジれる」といった違った方向に掛る力に対する剛性も、一本のチューブ内に持たせることができ、フレーム各部ごとに最適な特性を引き出すことができる。また、すべての工程が機械によるフルオートメーション化されたことで、製造されるすべてのフレームは高い品質を保持することが可能となっている。
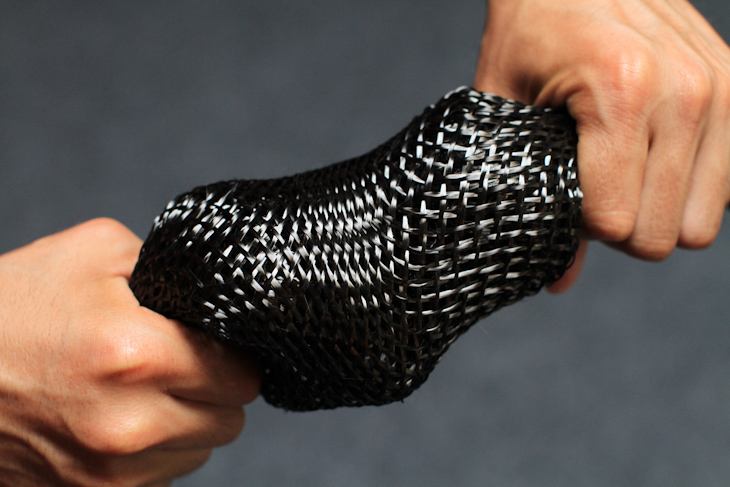
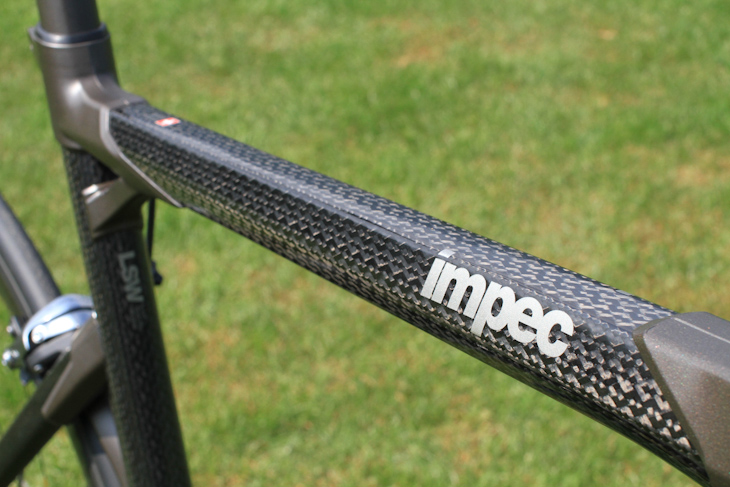
SNC
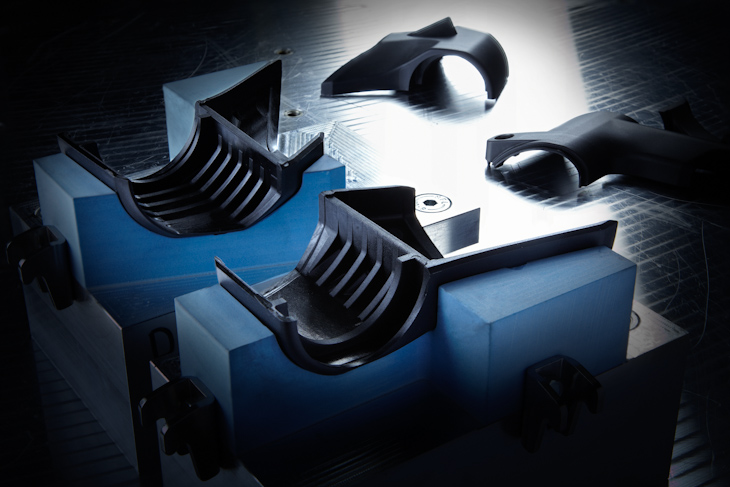
impecではLSWで製造されたシームレスパイプの特性を活かすために、パイプをシェルでつなぐという方法を採用。重量的にはシェル部分が加わることで、昨年のトップモデル“teammachine SLR01”よりやや重量増になったが、この製法によってより完璧な精度を実現している。また、右左のシェルはオス・メスに分かれていて、しっかりと両側からパイプをつかむように設計。さらに、すべてのシェルは光学検査された後、特殊な接着剤を使用して接合される。
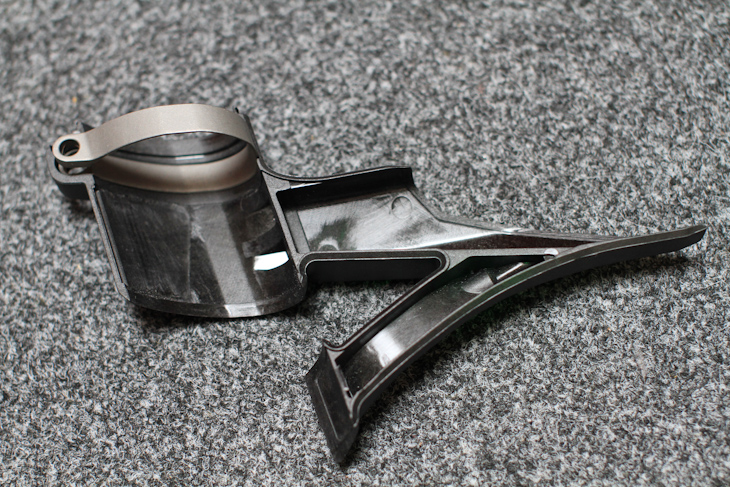
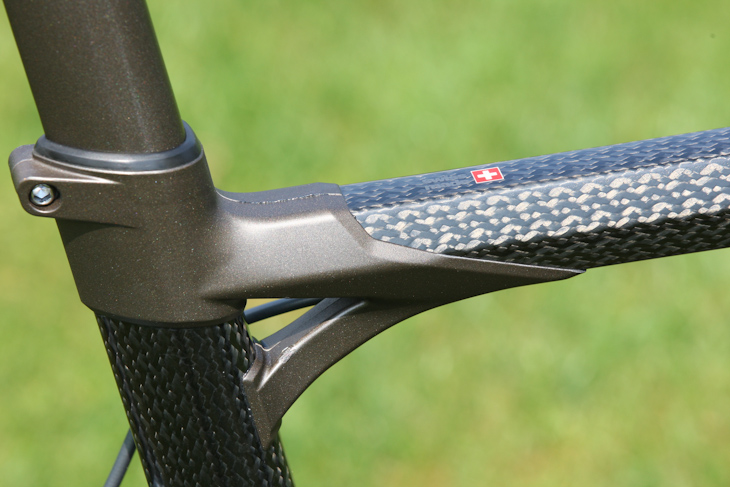
次のページではBMC本社にて行われたプレゼンテーションの模様を通じてimpecのテクノロジーとスペックを紹介する。
取材協力:フタバ商店 企画/制作:シクロワイアード テキスト:星野知大 写真:辻啓