第4世代ULTIMATE CF SLXの発表を前に世界各国のジャーナリストたちは、ドイツはコブレンツに構えられたキャニオンの本社とファクトリーを訪れた。そこで見たキャニオンの歴史、技術力を学ぶことができるショールームと、品質管理を徹底的に行なっていた工場の様子を紹介しよう。
ドイツ西部のコブレンツにキャニオンの本社とファクトリーはある
通路にも、これまで獲得したジャージが掲げられている
オフィスの至る所にキャニオンのバイクを駆り活躍した選手のポスターが掲げられている
本社のあるドイツ西部のコブレンツは、ドイツを代表する河川であるモーゼル川とライン川の合流地点に位置し、水と山に囲まれたのどかな街だ。街中から車を10分ほど走らせると白壁の巨大な施設が飛び込んでくる。これが2008年に建設されたキャニオン本社だ。ここにキャニオンが誇る高い製品開発力、製造、生産管理システムのすべてがあると言っていい。ここでは、その内部の様子を紹介していく。
まず、正面のエントランスを入ると、キャニオンの歴史を彩ってきた歴代の実車がお出迎え。“ピュアレーシング”を開発理念に据えるキャニオンらしい演出だ。レース熱心な創業者のローマン・アーノルド氏のバイクから、ロード界にキャニオンの名を轟かせたカデル・エヴァンスによる2009年の世界選手権優勝バイク。さらに、ナイロ・キンタナの2014年ジロ・デ・イタリア制覇の記念モデルなどが並ぶ。
エントランスを入ると創業者アーノルド氏のバイクが出迎えてくれる
創業者アーノルド氏が、レース会場でパーツを販売する際に使用していたカーキャリアも展示されていた
2009年の世界選手権を制したカデル・エヴァンスの実車も展示されている
3.785gの超軽量バイク「プロジェクト3.7」も並べられており、キャニオンの歴史を感じられる
続いて、歴史を感じさせる青色のカーキャリアが展示されている。これは、1985年創業のキャニオンの起源とも言える。創業者のローマン・アーノルド氏が、レース活動資金を得るためにイタリアやフランスのバイクパーツをドイツ国内のレース会場で販売するために使用していたカーキャリアである。その後、アーノルド氏はコブレンツ市内で自転車ショップを経営し、1996年にキャニオンを立ち上げるに至ったのだ。
カーキャリアと同じ空間には、その時代に掲げたプロジェクトを具現化し、ユーロバイクで発表してきたプロトタイプも展示される。2005年当時に発表した「プロジェクト3.7」は、3.785gの超軽量バイクだ。さらに奥には、エアロダイナミクスをはじめとするテクノロジーを紹介するスペースがある。ミュージアムのように楽しくキャニオンの歴史、テクノロジーを学ぶことができる。
テクノロジーを紹介するスペースがあり、ミュージアムのようにキャニオンについて学ぶことができる
ミュージアムのように楽しく歴史、テクノロジーを学ぶことができるキャニオン本社
ショールーム内にはダイレクトショップが設けられており、バイクを購入することができる
ここではキャニオン製の小物から他ブランドのアクセサリー類まで取り揃えられている
また、ショールーム内には、世界で唯一のダイレクトショップを併設する。バイクからオリジナルアイテム、他ブランドのアクセサリー類までが取り揃えられている。キャニオンユーザーでなくても利用でき、この日も多くのサイクリストが訪れていた。さらに、ショップ内にはカフェもありリラックスできる空間となっている。
2015年秋から稼働が開始される新工場は、全てがシステマチックになっている
また、ここは故障などでユーザーから持ち込まれたバイクを修理するメンテナンス部門として機能する。単なる生産工場だけでない点も、元々ショップ経営からスタートしたキャニオンらしい。キャニオン以外のバイクも対応していることも驚きだ。
しかし、このアッセンブルファクトリーをもってしても、近い将来、生産が追いつかなくなることを見越して、2年前から新工場の建設がはじまっていた。そして、いよいよ2015年秋から生産ラインを新工場へと完全移行する。新工場は、本社から車で15分ほどの場所にあり、こちらも広大な敷地に構える。
新工場は、当然ながら清潔感にあふれ、最新鋭の設備が整う。最大の特長は、膨大な数のストックパーツの管理からアッセンブルまでが、完全にシステマチックに制御されていることだ。
新工場の倉庫は膨大な量のパーツを保管することができる
バイクを組み上げるためのパーツは細かく管理されるという
出荷を待つバイクたちも整然と並べられている
1台1台のバイクにはQRコードが割り振られ、そこにはアッセンブルされるパーツが記憶される。パーツを管理するバックヤードのスタッフは、腕にそれらの情報を表示するタブレットとQRコードを読み取る赤外線センサーを取り付けて作業にあたる。タブレットからの情報をもとに、QRコードごとのケースにパーツを振り分けていく。キャニオンでは、購入の際にバイクによってはギヤの歯数などのパーツをカスタマイズできるが、データ管理により正確でかつ素早くパーツがチョイスすることを可能にする。
アッセンブルされるパーツが入ったケースは、フレーム、ホイール、フォークとともに、セクションごとに並んだラインの上で、組み付けられていく。各セクションにもタブレットが備え付けられ、そこからの情報をもとにスタッフは作業を進める。使用するトルクレンチは締め付けトルクがコンピューター上で管理されるなど、安定した品質管理を実現する。
スタッフはタブレットとQRコードリーダーを手にパーツ管理を行う
出荷専用のダンボールにもQRコードがラベリングされており、在庫から出荷まで管理される
使用するトルクレンチは締め付けトルクがコンピューター上で徹底的に管理されている
ホイールも1つ1つメカニックがパーツを組み込む
こうして走れる状態となった完成車は、工場内の試乗レーンでスタッフによる最終チェックが入る。その後、ハンドルとホイールを取り外して、専用の出荷用の段ボールケース(bikeguard)に収められる。出荷用のケースにもQRコードがラベリングされ、パーツの在庫管理から出荷状態のケースまで、コンピューターによって一元管理される。
新工場の誕生により、これまで以上に生産スピードが上がり、高品質なバイクを安定してユーザーの元へ届けることが可能になる。そして、納期の短縮も期待できるという。
これにより外見では見落とされてしまうフレーム製造時のエポキシ樹脂の気泡(ボイド)を見つけることを可能にした。こうしたカーボン製品のわずかな欠損は、落車時など衝撃がかかった際に、重大な事故につながりかねない。特に、特に、フロントフォークとカーボン製ハンドルバーについては全品検査を行うことでライダーの安全レベルを飛躍的に高めている。
フロントフォークは全品検査を行い、安全性を飛躍的に高めている
CTスキャンルームの横には、各パーツの強度や耐久性をチェックするラボが設置されている。耐久性を測る振動吸収テストや強度を測るインパクトテストを実施する機器はフォツイム大学と共同開発したオリジナル試験機だ。試験内容は、EN規格(欧州規格)の設定よりも厳しいキャニオン独自の合格基準を設けている。たとえば、ハンドルの振動耐久テストは、EN規格では5万回のところ12万回でクリアとなる。
このようにキャニオンでは、CTスキャンはじめ、数々の耐衝撃・耐久テストをクリアしたフレームに、自社で完璧にアッセンブルされた高品質なバイクだけが、ユーザーの手元へと届ける仕組みが確立されているのだ。
バイクを購入したコンシュマーがキャニオン社から梱包されたバイクを受け取ってから組み立てるまでの流れについては、こちらの公式ムービーでガイドされているので参考にして欲しい。
キャニオンの歴史を学べるミュージアムへ
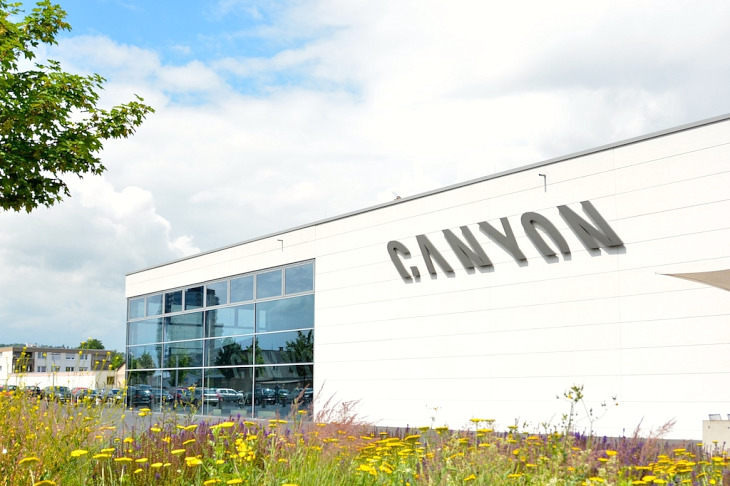
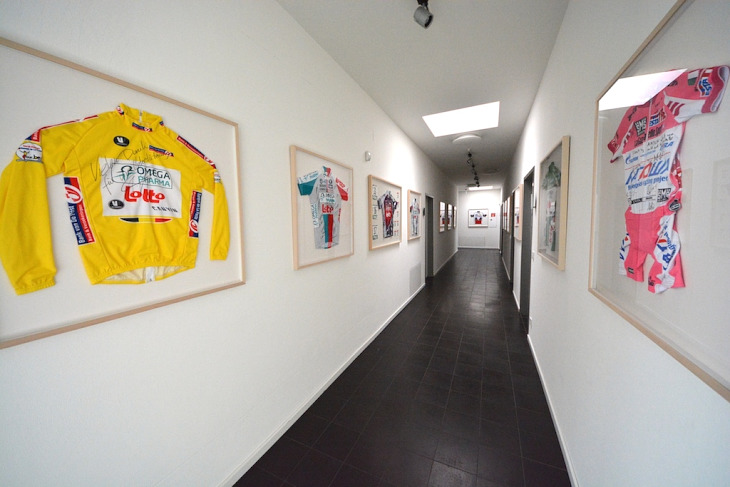
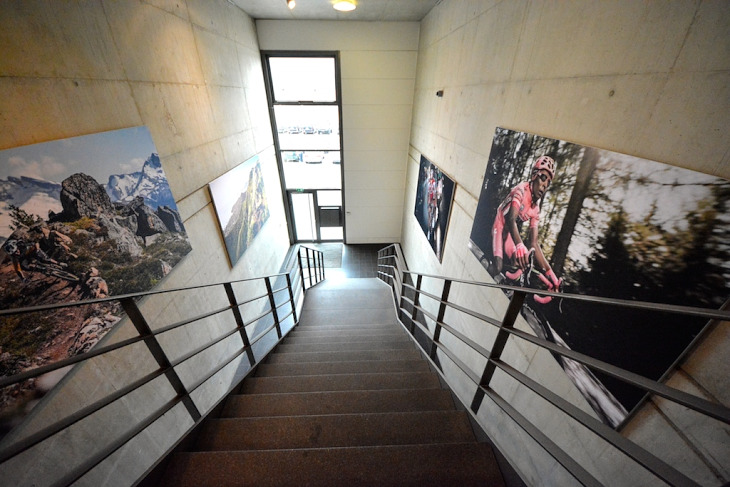
本社のあるドイツ西部のコブレンツは、ドイツを代表する河川であるモーゼル川とライン川の合流地点に位置し、水と山に囲まれたのどかな街だ。街中から車を10分ほど走らせると白壁の巨大な施設が飛び込んでくる。これが2008年に建設されたキャニオン本社だ。ここにキャニオンが誇る高い製品開発力、製造、生産管理システムのすべてがあると言っていい。ここでは、その内部の様子を紹介していく。
まず、正面のエントランスを入ると、キャニオンの歴史を彩ってきた歴代の実車がお出迎え。“ピュアレーシング”を開発理念に据えるキャニオンらしい演出だ。レース熱心な創業者のローマン・アーノルド氏のバイクから、ロード界にキャニオンの名を轟かせたカデル・エヴァンスによる2009年の世界選手権優勝バイク。さらに、ナイロ・キンタナの2014年ジロ・デ・イタリア制覇の記念モデルなどが並ぶ。
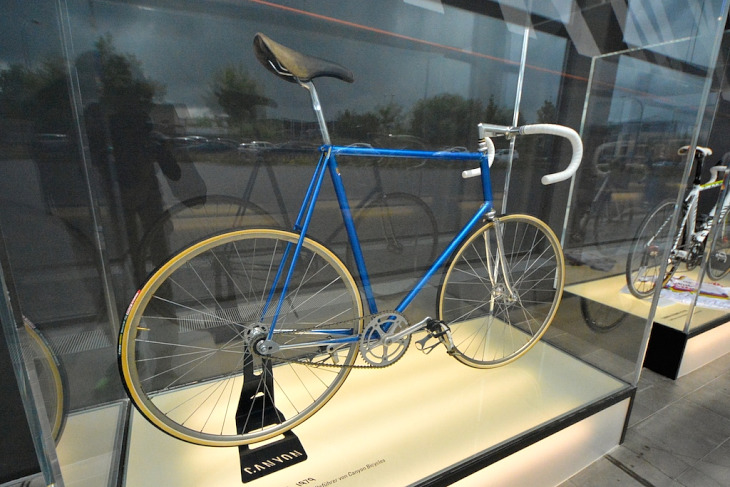
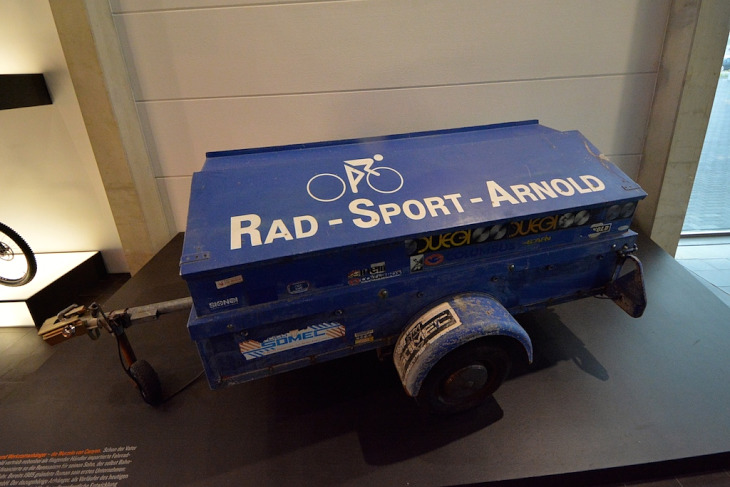
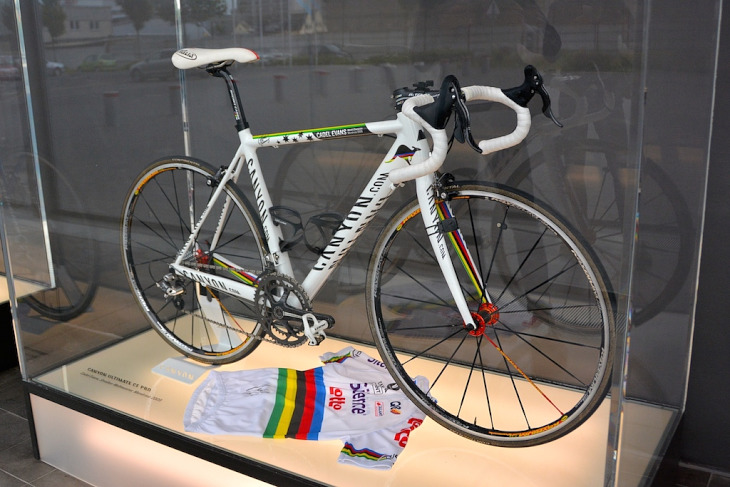
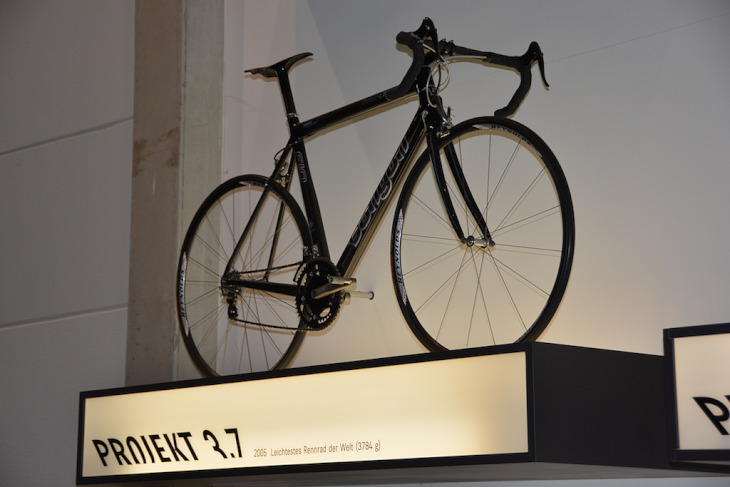
続いて、歴史を感じさせる青色のカーキャリアが展示されている。これは、1985年創業のキャニオンの起源とも言える。創業者のローマン・アーノルド氏が、レース活動資金を得るためにイタリアやフランスのバイクパーツをドイツ国内のレース会場で販売するために使用していたカーキャリアである。その後、アーノルド氏はコブレンツ市内で自転車ショップを経営し、1996年にキャニオンを立ち上げるに至ったのだ。
カーキャリアと同じ空間には、その時代に掲げたプロジェクトを具現化し、ユーロバイクで発表してきたプロトタイプも展示される。2005年当時に発表した「プロジェクト3.7」は、3.785gの超軽量バイクだ。さらに奥には、エアロダイナミクスをはじめとするテクノロジーを紹介するスペースがある。ミュージアムのように楽しくキャニオンの歴史、テクノロジーを学ぶことができる。
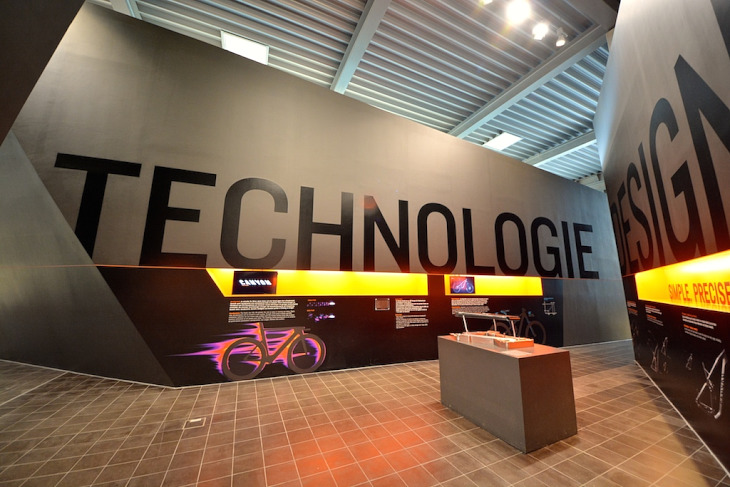
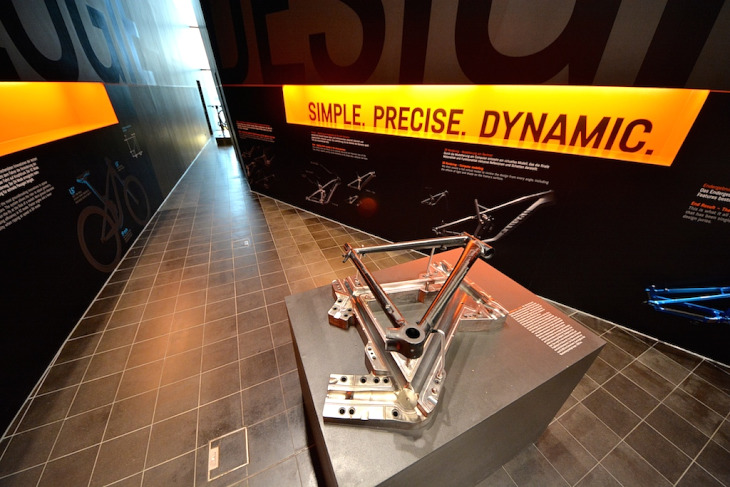
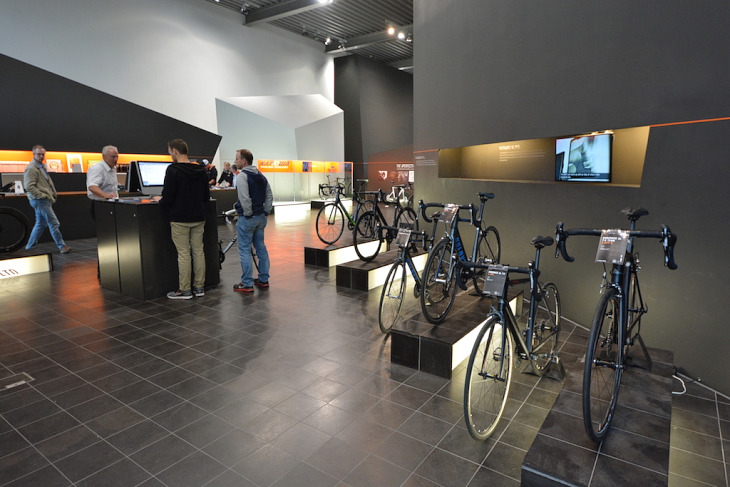
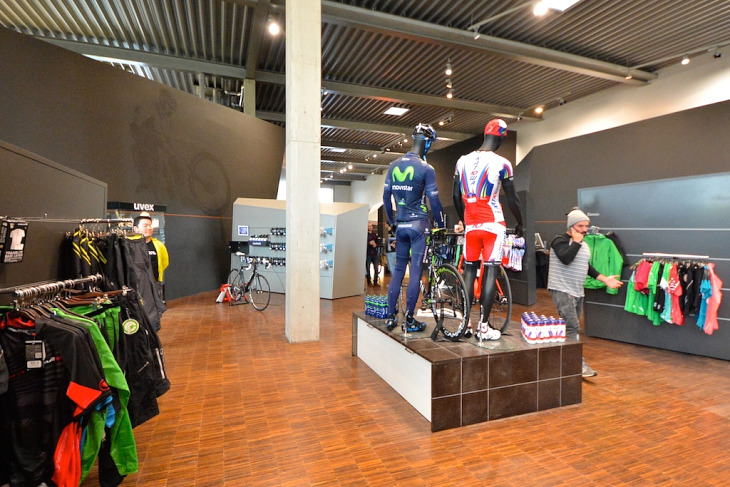
また、ショールーム内には、世界で唯一のダイレクトショップを併設する。バイクからオリジナルアイテム、他ブランドのアクセサリー類までが取り揃えられている。キャニオンユーザーでなくても利用でき、この日も多くのサイクリストが訪れていた。さらに、ショップ内にはカフェもありリラックスできる空間となっている。
生産管理をコンピューター制御する新工場が誕生
この広々としたショールームも巨大な施設の一部にすぎない。ショールームの裏側に通されると、そこには作業台座が並び、職人たちが黙々とバイクのアッセンブルを行なう空間が広がっていた。この場所こそ、2008年以来、キャニオンの生産ラインを支えてきた心臓部だ。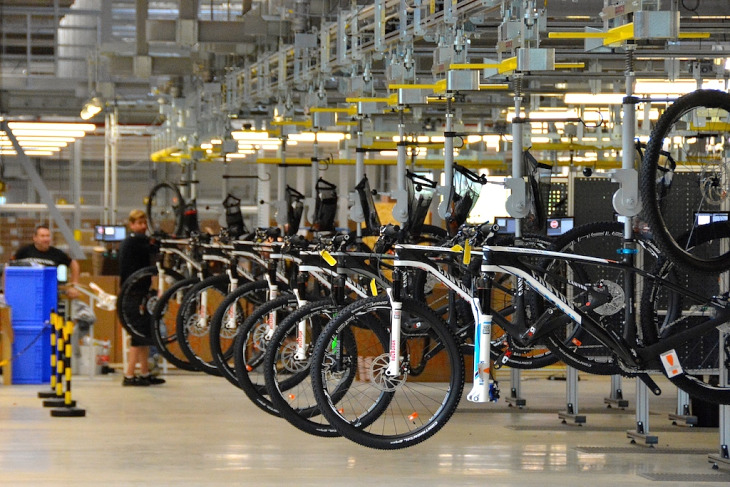
また、ここは故障などでユーザーから持ち込まれたバイクを修理するメンテナンス部門として機能する。単なる生産工場だけでない点も、元々ショップ経営からスタートしたキャニオンらしい。キャニオン以外のバイクも対応していることも驚きだ。
しかし、このアッセンブルファクトリーをもってしても、近い将来、生産が追いつかなくなることを見越して、2年前から新工場の建設がはじまっていた。そして、いよいよ2015年秋から生産ラインを新工場へと完全移行する。新工場は、本社から車で15分ほどの場所にあり、こちらも広大な敷地に構える。
新工場は、当然ながら清潔感にあふれ、最新鋭の設備が整う。最大の特長は、膨大な数のストックパーツの管理からアッセンブルまでが、完全にシステマチックに制御されていることだ。
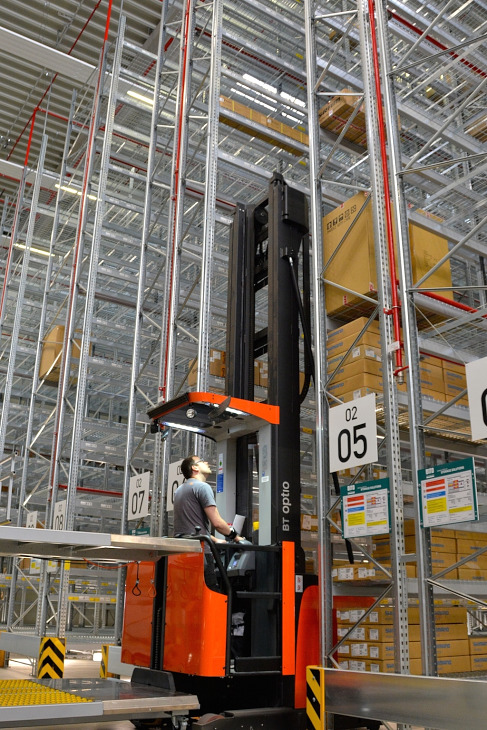
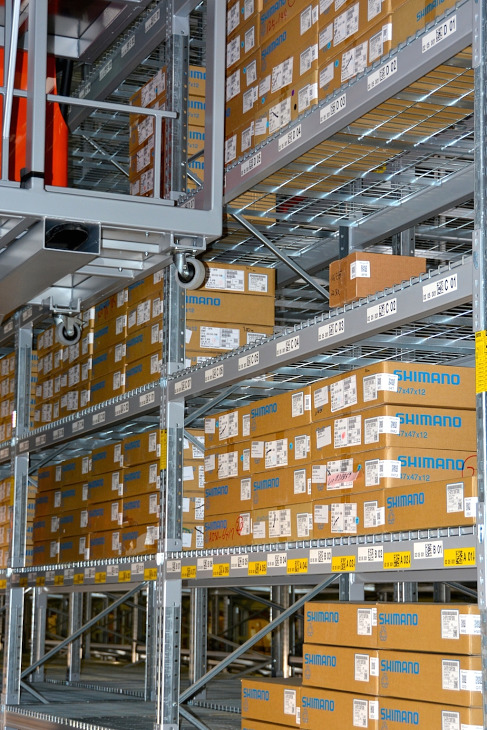
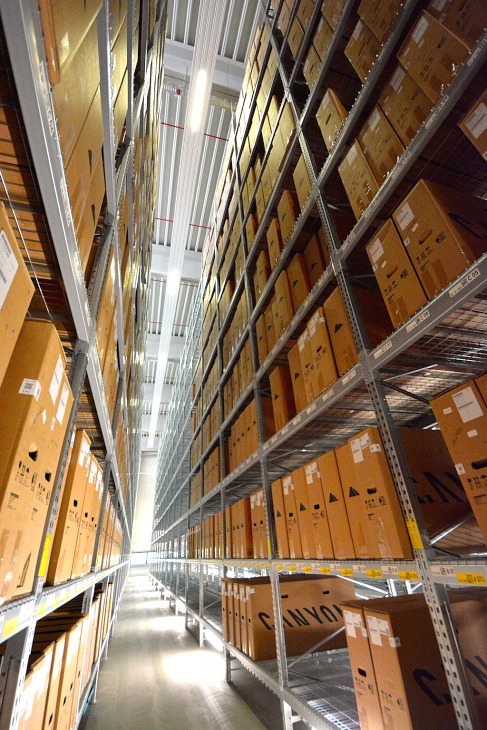
1台1台のバイクにはQRコードが割り振られ、そこにはアッセンブルされるパーツが記憶される。パーツを管理するバックヤードのスタッフは、腕にそれらの情報を表示するタブレットとQRコードを読み取る赤外線センサーを取り付けて作業にあたる。タブレットからの情報をもとに、QRコードごとのケースにパーツを振り分けていく。キャニオンでは、購入の際にバイクによってはギヤの歯数などのパーツをカスタマイズできるが、データ管理により正確でかつ素早くパーツがチョイスすることを可能にする。
アッセンブルされるパーツが入ったケースは、フレーム、ホイール、フォークとともに、セクションごとに並んだラインの上で、組み付けられていく。各セクションにもタブレットが備え付けられ、そこからの情報をもとにスタッフは作業を進める。使用するトルクレンチは締め付けトルクがコンピューター上で管理されるなど、安定した品質管理を実現する。
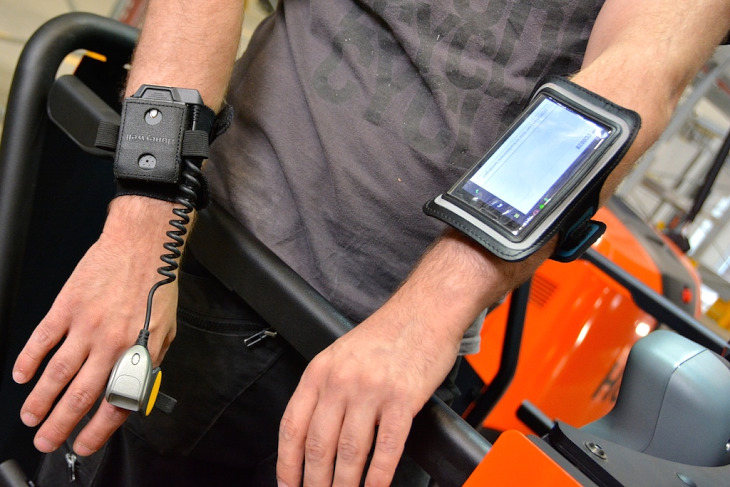
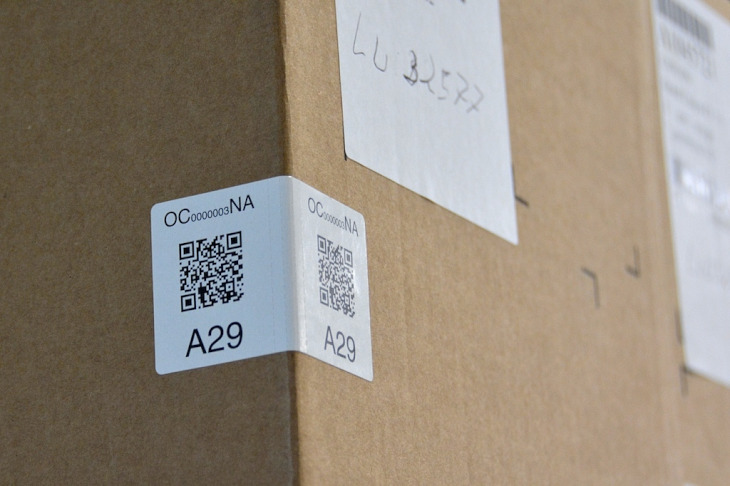
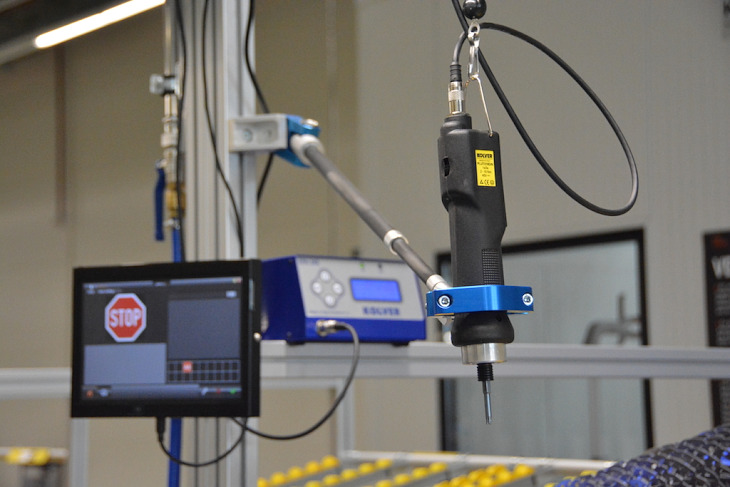
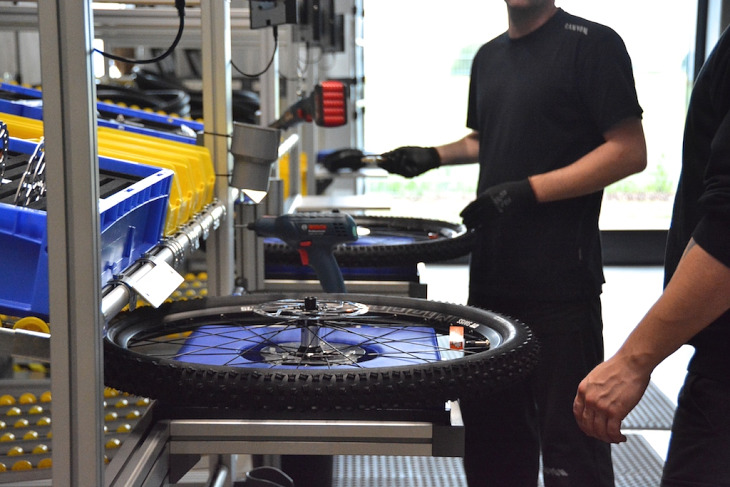
こうして走れる状態となった完成車は、工場内の試乗レーンでスタッフによる最終チェックが入る。その後、ハンドルとホイールを取り外して、専用の出荷用の段ボールケース(bikeguard)に収められる。出荷用のケースにもQRコードがラベリングされ、パーツの在庫管理から出荷状態のケースまで、コンピューターによって一元管理される。
新工場の誕生により、これまで以上に生産スピードが上がり、高品質なバイクを安定してユーザーの元へ届けることが可能になる。そして、納期の短縮も期待できるという。
高品質を支えるCTスキャンと厳格なテスト
高品質なバイクを生み出すキャニオンは、フレームの開発設計とパーツアッセンブルの全行程を自社で一貫して行なっている。さらに、徹底してレーム、フォーク、ハンドルのカーボンパーツの品質管理を追求するため、業界でもイチ早く工業用CTスキャン機器(エクスロン社製)を導入したメーカーとして知られる。これにより外見では見落とされてしまうフレーム製造時のエポキシ樹脂の気泡(ボイド)を見つけることを可能にした。こうしたカーボン製品のわずかな欠損は、落車時など衝撃がかかった際に、重大な事故につながりかねない。特に、特に、フロントフォークとカーボン製ハンドルバーについては全品検査を行うことでライダーの安全レベルを飛躍的に高めている。
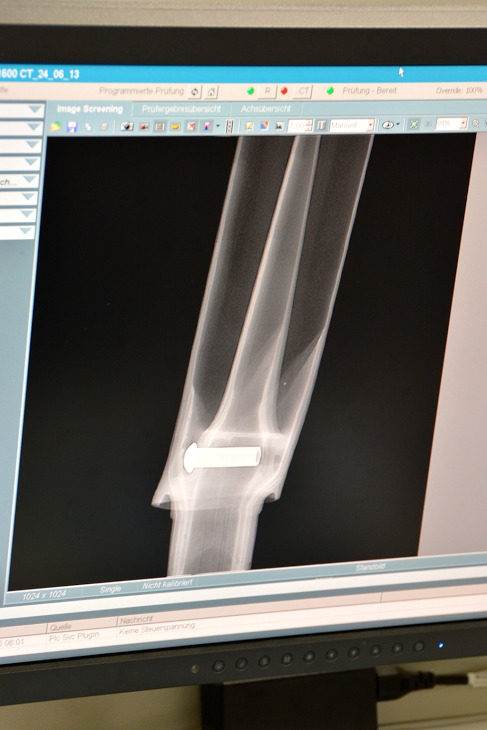
CTスキャンルームの横には、各パーツの強度や耐久性をチェックするラボが設置されている。耐久性を測る振動吸収テストや強度を測るインパクトテストを実施する機器はフォツイム大学と共同開発したオリジナル試験機だ。試験内容は、EN規格(欧州規格)の設定よりも厳しいキャニオン独自の合格基準を設けている。たとえば、ハンドルの振動耐久テストは、EN規格では5万回のところ12万回でクリアとなる。
このようにキャニオンでは、CTスキャンはじめ、数々の耐衝撃・耐久テストをクリアしたフレームに、自社で完璧にアッセンブルされた高品質なバイクだけが、ユーザーの手元へと届ける仕組みが確立されているのだ。
バイクを購入したコンシュマーがキャニオン社から梱包されたバイクを受け取ってから組み立てるまでの流れについては、こちらの公式ムービーでガイドされているので参考にして欲しい。
提供:キャニオン・ジャパン photo/text:Kenji.Hashimoto 制作:シクロワイアード編集部